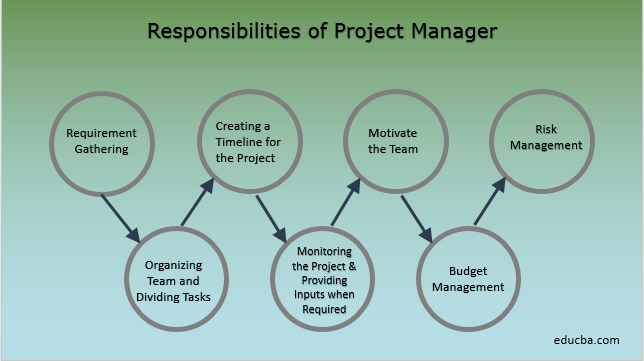
The team manager oversees a group. They make sure that everyone is on task and balance their workload. They also deal with conflict between team members and provide constructive feedback. The most successful managers know how to balance their work with their team members' needs. These qualities make team management effective. These attributes can be used to inspire and increase morale among team members.
Leadership skills
A key ingredient for being a team manager is leadership skills. Team leaders must have strategic thinking and be able to translate long-term organizational goals into tangible results. Leaders without this skill are likely to run into problems that will harm the organization long-term. They will lose sight of the importance of their team to the organization and their own role in it. A leader who is able to think strategically must look beyond the immediate issues in order to see the organizational goals and the complexity of internal and externe factors.
The ability to communicate with and be accessible to other members of the team is a key characteristic for leaders. Openly listening is an essential skill in leadership because it shows that you understand other people's viewpoints and can listen to their concerns before you decide how to deal with them. This skill allows your team to be motivated and recognize their input.
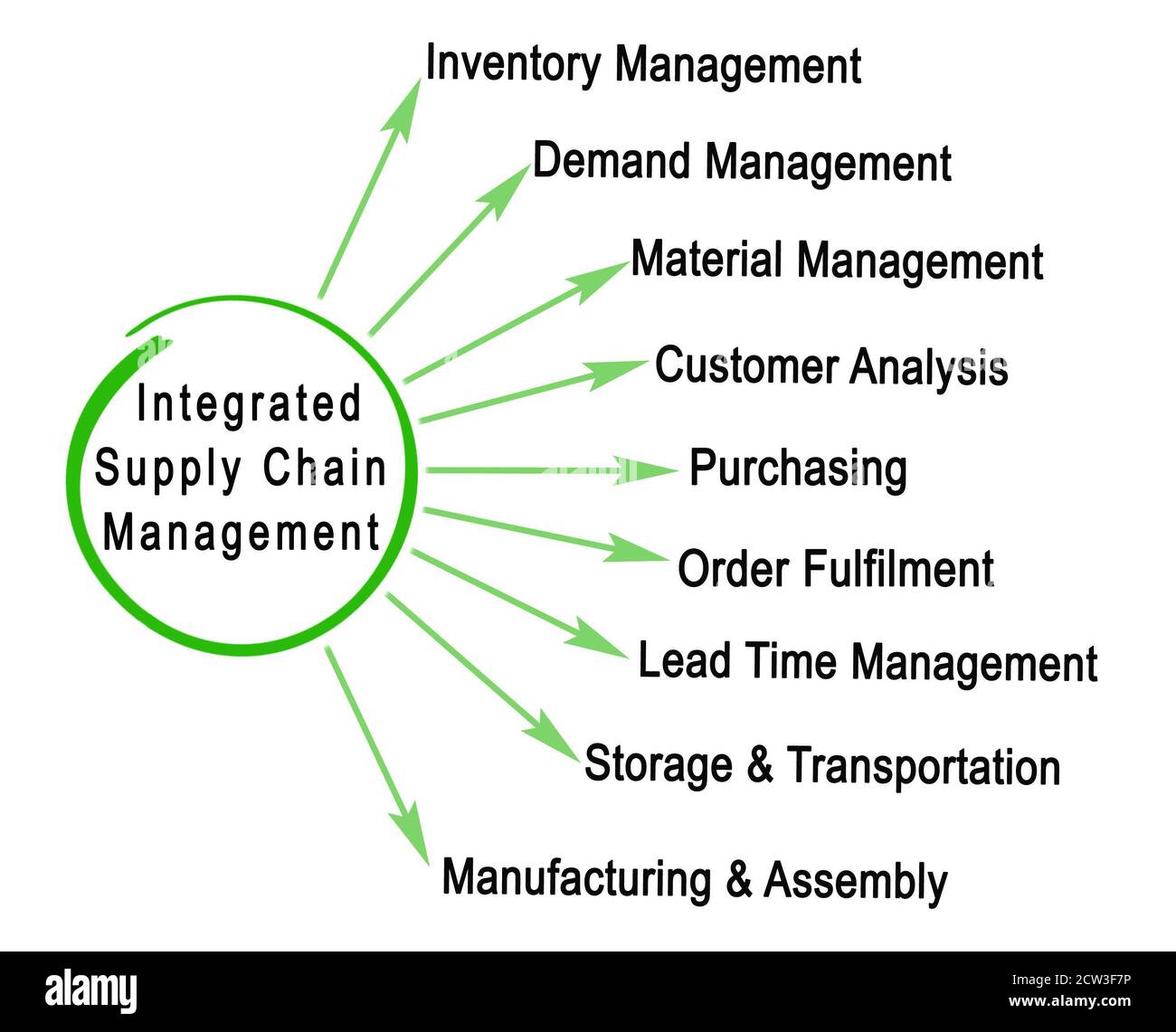
Communication skills
Communication skills are critical in the workplace as well as in managing a team. A lack of communication skills can be a significant barrier to an organization's success. According to a Gatehouse report, poor communication among managers was the top three cause of ineffective internal communication. Also, only 14% of employees stated that their performance reviews inspired them. Managers must be able to communicate with their team and build relationships. Managers can do this by listening to their team and clarifying their ideas and points of view.
Communicating with people effectively is by being direct and sincere with them. Different employees prefer details, while others prefer generalizations. Knowing which communication style your team prefers will help you adjust your communication style. The more you pay attention to your team's communication preferences the more they will feel heard and understood.
Skills in organization
Organization skills are crucial if you want to manage a team. These skills help you to manage time, people, and conflict. Your ability to organize and prioritize tasks will give you credibility and make you more trustworthy. If you are able to organize your thoughts and solve problems, you will be able to analyze complex situations and find solutions. You'll also be more calm under pressure when you are well-organized.
You will communicate better with your colleagues if you have better organization skills. It will also help you spend more time on your most important tasks. Your workspace will make you less productive and could cause stress. To keep your workspace organized, rewrite the to-do list.
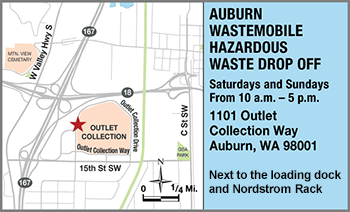
Time management
A key component of team management is good time management. This involves regular check-ins as well the use tools to track each project's progress. Encourage team members to be productive, and celebrate their achievements. You can increase productivity of your team and avoid overload by practicing time management.
Whatever the size of your team or organization, time management is essential to the success your company. A time management strategy that works requires flexibility and adaptability to change. This can be achieved by aligning your teams. According to studies, teams spend two-thirds their time communicating, connecting, or collaborating. Inefficient communication can also lead to 15 percent less employee time.
FAQ
What are the most important management skills?
Managerial skills are crucial for every business owner, regardless of whether they run a small store in their locality or a large corporation. These skills include the ability of managing people, finances, time, space, and other factors.
You will need management skills to set goals and objectives, plan strategies, motivate employees, resolve problems, create policies and procedures, and manage change.
As you can see, there's no end to the list of managerial duties!
What is Six Sigma and how can it help you?
It's a strategy for quality improvement that emphasizes customer care and continuous learning. The objective is to eliminate all defects through statistical methods.
Six Sigma was developed at Motorola in 1986 as part of its efforts to improve manufacturing processes.
The idea spread quickly throughout the industry, and today, many organizations are using six sigma methods to improve product design, production, delivery, and customer service.
What can a manager do to improve his/her management skillset?
Through demonstrating good management skills at every opportunity
Managers must continuously monitor the performance levels of their subordinates.
You must quickly take action if your subordinate fails to perform.
You must be able to spot what is lacking and how you can improve it.
What are some common mistakes managers make?
Sometimes managers make it harder for their employees than is necessary.
They may not delegate enough responsibilities to staff and fail to give them adequate support.
Many managers lack the communication skills to motivate and lead their employees.
Some managers create unrealistic expectations for their teams.
Some managers may try to solve every problem themselves instead of delegating responsibility to others.
Statistics
- Hire the top business lawyers and save up to 60% on legal fees (upcounsel.com)
- UpCounsel accepts only the top 5 percent of lawyers on its site. (upcounsel.com)
- 100% of the courses are offered online, and no campus visits are required — a big time-saver for you. (online.uc.edu)
- This field is expected to grow about 7% by 2028, a bit faster than the national average for job growth. (wgu.edu)
- Our program is 100% engineered for your success. (online.uc.edu)
External Links
How To
How can Lean Manufacturing be done?
Lean Manufacturing methods are used to reduce waste through structured processes. They were created by Toyota Motor Corporation in Japan in the 1980s. The goal was to produce quality products at lower cost. Lean manufacturing emphasizes removing unnecessary steps from the production process. It consists of five basic elements: pull systems, continuous improvement, just-in-time, kaizen (continuous change), and 5S. Pull systems are able to produce exactly what the customer requires without extra work. Continuous improvement involves constantly improving upon existing processes. Just-in–time refers when components or materials are delivered immediately to their intended destination. Kaizen means continuous improvement. Kaizen involves making small changes and improving continuously. Finally, 5S stands for sort, set in order, shine, standardize, and sustain. These five elements work together to produce the best results.
The Lean Production System
Six key concepts make up the lean manufacturing system.
-
Flow - focus on moving material and information as close to customers as possible;
-
Value stream mapping is the ability to divide a process into smaller tasks, and then create a flowchart that shows the entire process.
-
Five S's - Sort, Set In Order, Shine, Standardize, and Sustain;
-
Kanban - visual cues such as stickers or colored tape can be used to track inventory.
-
Theory of constraints: identify bottlenecks in your process and eliminate them using lean tools, such as kanban board.
-
Just-in-time - deliver components and materials directly to the point of use;
-
Continuous improvement - incremental improvements are made to the process, not a complete overhaul.