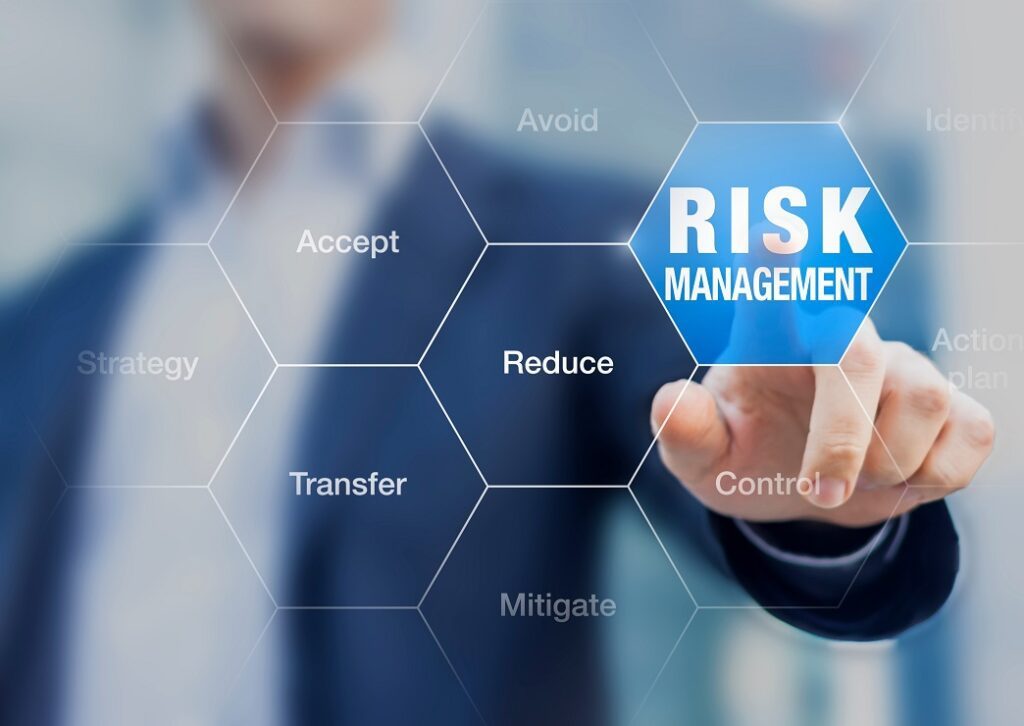
Timekeeping may be something you are used to as an employee. It is a great way to track and record the time that you spend doing a job. It is also a great way to get important business data, which can prove useful in performance analysis and improvement. Time records can help you identify key trends, such the efficiency or cost of a process. Modern businesses are familiar with timekeeping systems. There are many different types of timekeeping software.
Become a timekeeper
A timekeeper is a good option for those who love sports and want a positive impact on the community. This job requires you to be able to communicate effectively with others and have excellent organizational skills. This job is extremely rewarding and allows you to interact with people from many industries. A career as a timekeeper can offer many benefits.
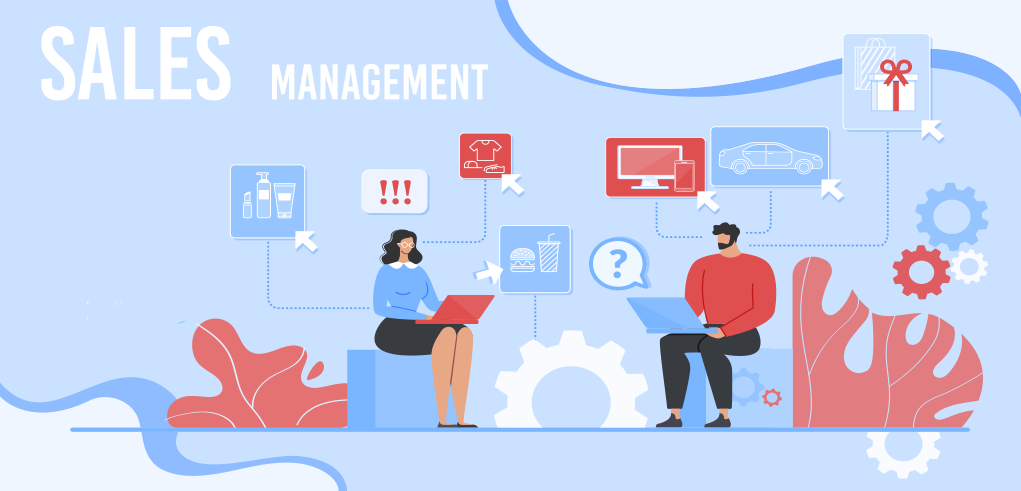
Be a timekeeper in your company
A timekeeper position at a company can bring many benefits. Although these jobs do not require a college diploma, they require excellent computer skills and attention. You will need to be flexible and work well under tight deadlines. A manager position is possible if you are good with numbers, and you have great record-keeping skills. These jobs offer the opportunity to move up in your career.
Use a timekeeping program to help you organize your work.
A timekeeping program will enhance your company's productivity. It will allow you to comply with all legal requirements, and keep track of the hours worked by your employees. Timekeeping software will also help you meet your budget and analyze employee performance. You can analyze employee performance data to determine what tasks need more time. Timekeeping software that is reliable will let you assign tasks and track the progress of your team members. Timekeeping software may even allow you add comments to each entry.
Timekeeper for a mobile App
Becoming a timekeeper for your mobile app is a great way to stay organized, no matter if you work freelance or own a company. It will help you track time spent on tasks by employees and will save you time filling out paper timesheets. An app that tracks employee hours can be used to track projects. It is also accessible via the internet from any place with an internet connection.
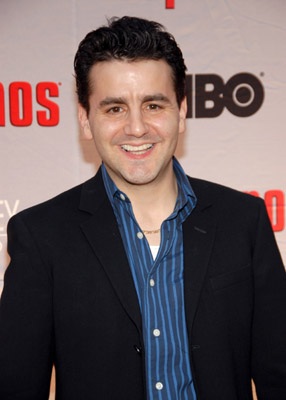
Use a biometric timeclock to work
Biometric time clocks allow you to track employee hours more effectively. This can help reduce time spent in the line waiting to punch in and out. It can also reduce the risk of time theft. The biometric clock can help reduce payroll costs by up to 10%. It tracks fingerprints of employees and determines how long they have been at work. This means that your employees will never be late for work again.
FAQ
What are the main four functions of management
Management is responsible to plan, organize, direct, and control people and resources. This includes setting goals, developing policies and procedures, and creating procedures.
Management aids an organization in reaching its goals by providing direction and coordination, control, leadership motivation, supervision, training, evaluation, and leadership.
The four main functions of management are:
Planning - This is the process of deciding what should be done.
Organizing - Organizing involves deciding how things should be done.
Direction - This is the art of getting people to follow your instructions.
Controlling - This is the ability to control people and ensure that they do their jobs according to plan.
What are the five management processes?
These five stages are: planning, execution monitoring, review and evaluation.
Setting goals for the future is part of planning. It includes defining what you want to achieve and how you plan to do it.
Execution is the actual execution of the plans. These plans must be adhered to by everyone.
Monitoring is checking on progress towards achieving your objectives. Regular reviews of performance against targets, budgets, and other goals should be part.
Reviews take place at the end of each year. They provide an opportunity to assess whether everything went well during the year. If not, it is possible to make improvements for next year.
After each year's review, evaluation occurs. It helps identify what worked well and what didn't. It also provides feedback on how well people performed.
What does it mean to say "project management"
Management is the act of managing activities in order to complete a project.
We help you define the scope of your project, identify the requirements, prepare the budget, organize the team, plan the work, monitor progress and evaluate the results before closing down the project.
What is TQM and how can it help you?
The industrial revolution led to the birth and growth of the quality movement. Manufacturing companies realized they couldn't compete solely on price. If they wanted to stay competitive, they needed to improve their quality and efficiency.
Management responded to the need to improve, and developed Total Quality Management (TQM). This focused on improving every aspect of an organization’s performance. It included continuous improvement, employee involvement and customer satisfaction.
What's the difference between leadership & management?
Leadership is about influencing others. Management is about controlling others.
A leader inspires followers while a manager directs workers.
A leader motivates people and keeps them on task.
A leader develops people; a manager manages people.
What are the steps involved in making a decision in management?
The decision-making process for managers is complex and multifaceted. It involves many elements, including analysis, strategy. planning. implementation. measurement. evaluation. feedback.
The key thing to remember when managing people is that they are human beings just as you are and therefore make mistakes. There is always room to improve, especially if your first priority is to yourself.
In this video, we explain what the decision-making process looks like in Management. We will discuss the various types of decisions, and why they are so important. Every manager should be able to make them. The following topics will be covered:
Statistics
- 100% of the courses are offered online, and no campus visits are required — a big time-saver for you. (online.uc.edu)
- The profession is expected to grow 7% by 2028, a bit faster than the national average. (wgu.edu)
- As of 2020, personal bankers or tellers make an average of $32,620 per year, according to the BLS. (wgu.edu)
- Your choice in Step 5 may very likely be the same or similar to the alternative you placed at the top of your list at the end of Step 4. (umassd.edu)
- UpCounsel accepts only the top 5 percent of lawyers on its site. (upcounsel.com)
External Links
How To
How does Lean Manufacturing work?
Lean Manufacturing uses structured methods to reduce waste, increase efficiency and reduce waste. They were developed by Toyota Motor Corporation in Japan during the 1980s. The goal was to produce quality products at lower cost. Lean manufacturing is about eliminating redundant steps and activities from the manufacturing process. It is made up of five elements: continuous improvement, continuous improvement, just in-time, continuous change, and 5S. The production of only what the customer needs without extra work is called pull systems. Continuous improvement is constantly improving upon existing processes. Just-in time refers to components and materials being delivered right at the place they are needed. Kaizen stands for continuous improvement. Kaizen can be described as a process of making small improvements continuously. The 5S acronym stands for sort in order, shine standardize and maintain. These five elements are combined to give you the best possible results.
Lean Production System
Six key concepts underlie the lean production system.
-
Flow is about moving material and information as near as customers can.
-
Value stream mapping: This is a way to break down each stage into separate tasks and create a flowchart for the entire process.
-
Five S’s - Sorted, In Order. Shine. Standardize. And Sustain.
-
Kanban – visual signals like colored tape, stickers or other visual cues are used to keep track inventory.
-
Theory of constraints - identify bottlenecks in the process and eliminate them using lean tools like kanban boards;
-
Just-in Time - Send components and material directly to the point-of-use;
-
Continuous improvement is making incremental improvements to your process, rather than trying to overhaul it all at once.