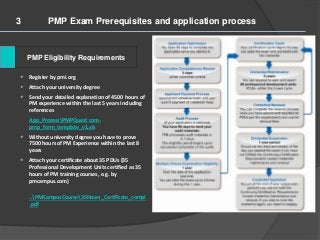
An essential tool to determine if your business is vulnerable to potential dangers is the risk assessment. The process of performing a risk assessment should be repeated regularly. This will provide you with a snapshot of current risks and threats to your system. Do a risk assessment on your application portfolio. Document security requirements, network diagrams. Data stored or transmitted by systems. Interactions with external services. Physical assets.
Hazard identification
It is crucial to identify hazards in risk assessments. Many people don't have the skills required to identify hazards correctly, so some legitimate risks may be overlooked. An anchor can help increase the number of people who are trained to recognize hazards. It also helps reduce the chances that an unidentified risk is overlooked. This study examined 72 participants randomly assigned as high-anchor or lower-anchor conditions and administered a personality assessment based on five factors.
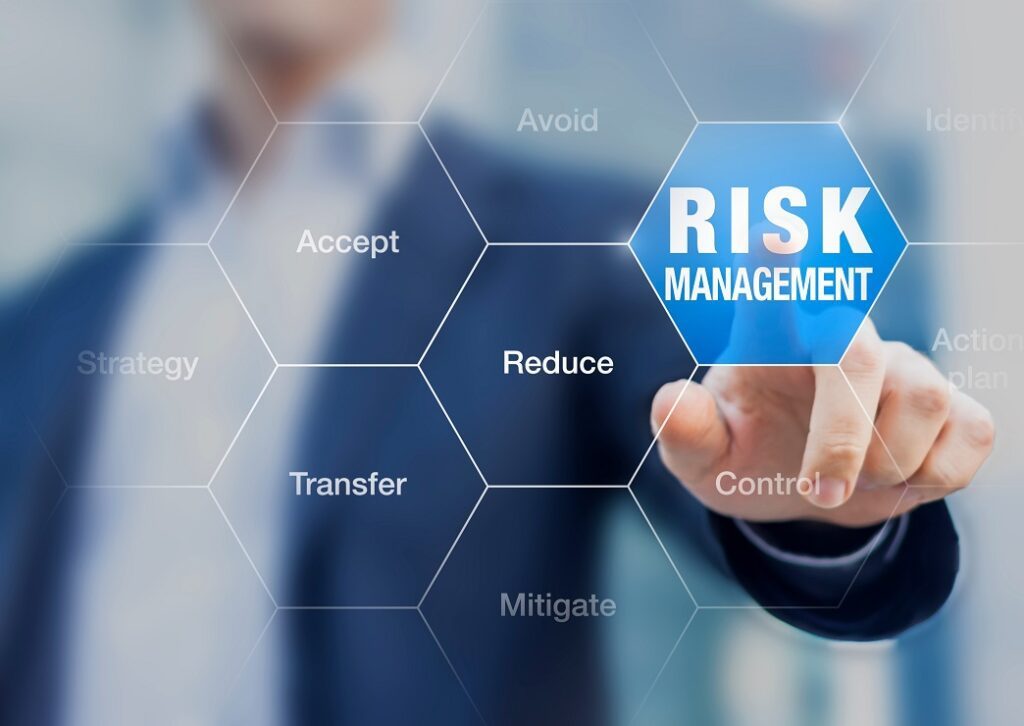
Review of documents
Ling is an aspiring project manager for a large internet business. Her first project involves the creation of privacy software solutions to a client. To identify project risks, Ling will use documentation reviews. Document review involves a structured review of a project's plans, assumptions, and available information. These findings will be used to inform the risk assessment process. Documentation review is a great way to reduce risk exposure.
Influence diagrams
An effective tool for organizing a sequence, influence diagrams are useful. These diagrams are often used in risk management, project management, and other organizational disciplines. The use of influence diagrams allows participants to visualize the connections between different factors or actions, and the potential for harm or losses. They are also a useful tool for assessing the risks associated with particular projects. These diagrams can be used to illustrate and group work.
Impact diagrams
Impact diagrams are a valuable tool for assessing the relative risks associated with a project. They show the effect of each risk on the project. This analysis is typically performed by the risk manager or people who are familiar with the risks. The results of the analysis can be ranked according to impact, duration uncertainty and probability of occurrence. The diagrams can be used to determine which risks need to be addressed first and which ones should be revised.
iAuditor
iAuditor digital tool for risk assessment replaces pen and hand checklists with digital reporting. This software will make your risk assessment processes easier and more efficient. Free templates are available to help you get started. The checklists can be customized to meet your needs. Next, you can assign corrective action to your workers. Comprehensive reports will automatically be generated after the assessment is complete and saved in your account. These reports may be shared with other users and can be modified whenever necessary.

Corrective action
Corrective actions are taken to address a real or potential risk. The process can be lengthy and time-consuming. It is essential to monitor the results to ensure that the corrective action is successful. Corrective measures are not isolated events. They are part and parcel of the overall process. Tracking the progress of corrective actions helps you identify issues and determine which ones are best addressed. This will help you improve your overall performance.
FAQ
What is a fundamental management tool for decision-making?
The decision matrix is a powerful tool that managers can use to help them make decisions. It allows them to consider all possible solutions.
A decision matrix can be used to show alternative options as rows or columns. This makes it easy for you to see how each option affects other options.
The boxes on the left hand side of this matrix represent four possible choices. Each box represents an option. The status quo (the current condition) is shown in the top row, and what would happen if there was no change?
The effect of Option 1 can be seen in the middle column. In this case, it would mean increasing sales from $2 million to $3 million.
These are the results of selecting Options 2 or 3. These are both positive changes that increase sales by $1million and $500,000. However, these also involve negative consequences. Option 2, for example, increases the cost by $100 000 while Option 3 decreases profits by $200 000.
The last column shows you the results of Option 4. This results in a decrease of sales by $1,000,000
The best thing about using a decision matrix is that you don't need to remember which numbers go where. You just look at the cells and know immediately whether any given a choice is better than another.
This is because your matrix has already done the hard work. It is as simple a matter of comparing all the numbers in each cell.
Here's an example showing how you might use a Decision Matrix in your business.
It is up to you to decide whether to spend more money on advertising. This will allow you to increase your revenue by $5000 per month. But, you will also incur additional expenses of $10 thousand per month.
The net result of advertising investment can be calculated by looking at the cell below that reads "Advertising." It is 15 thousand. Therefore, you should choose to invest in advertising since it is worth more than the cost involved.
What does the term "project management” mean?
Management is the act of managing activities in order to complete a project.
This includes defining the scope, identifying the requirements and preparing the budget. We also organize the project team, schedule the work, monitor progress, evaluate results, and close the project.
What is Kaizen, exactly?
Kaizen is a Japanese term for "continuous improvement." It encourages employees constantly to look for ways that they can improve their work environment.
Kaizen is built on the belief that everyone should be able do their jobs well.
What are the main management skills?
Management skills are essential for any business owner, whether they're running a small local store or an international corporation. These skills include the ability of managing people, finances, time, space, and other factors.
You will need management skills to set goals and objectives, plan strategies, motivate employees, resolve problems, create policies and procedures, and manage change.
You can see that there are many managerial duties.
Which kind of people use Six Sigma
Six sigma is a common concept for people who have worked in statistics or operations research. It can be used by anyone in any business aspect.
This requires a lot of dedication, so only people with great leadership skills can make the effort to implement it.
Statistics
- Our program is 100% engineered for your success. (online.uc.edu)
- This field is expected to grow about 7% by 2028, a bit faster than the national average for job growth. (wgu.edu)
- UpCounsel accepts only the top 5 percent of lawyers on its site. (upcounsel.com)
- As of 2020, personal bankers or tellers make an average of $32,620 per year, according to the BLS. (wgu.edu)
- Hire the top business lawyers and save up to 60% on legal fees (upcounsel.com)
External Links
How To
How does Lean Manufacturing work?
Lean Manufacturing is a method to reduce waste and increase efficiency using structured methods. These processes were created by Toyota Motor Corporation, Japan in the 1980s. It was designed to produce high-quality products at lower prices while maintaining their quality. Lean manufacturing is about eliminating redundant steps and activities from the manufacturing process. It is composed of five fundamental elements: continuous improvement; pull systems, continuous improvements, just-in–time, kaizen, continuous change, and 5S. Pull systems involve producing only what the customer wants without any extra work. Continuous improvement is constantly improving upon existing processes. Just-intime refers the time components and materials arrive at the exact place where they are needed. Kaizen refers to continuous improvement. It is achieved through small changes that are made continuously. Fifth, the 5S stand for sort, set up in order to shine, standardize, maintain, and standardize. These five elements can be combined to achieve the best possible results.
The Lean Production System
The lean production system is based on six key concepts:
-
Flow is about moving material and information as near as customers can.
-
Value stream mapping is the ability to divide a process into smaller tasks, and then create a flowchart that shows the entire process.
-
Five S's: Sort, Shine Standardize, Sustain, Set In Order, Shine and Shine
-
Kanban – visual signals like colored tape, stickers or other visual cues are used to keep track inventory.
-
Theory of constraints: Identify bottlenecks and use lean tools such as kanban boards to eliminate them.
-
Just-in-time - deliver components and materials directly to the point of use;
-
Continuous improvement: Make incremental improvements to the process instead of overhauling it completely.