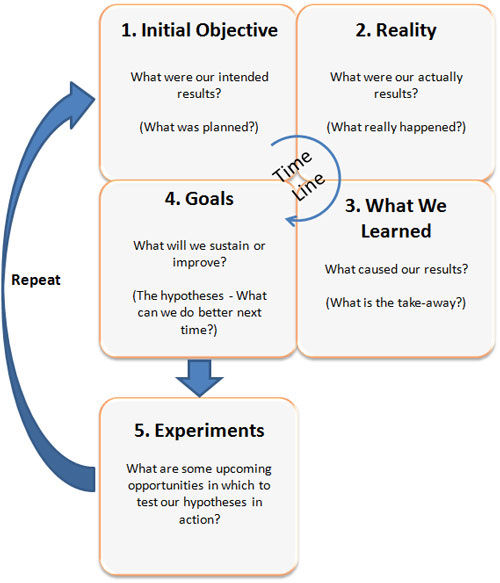
Waste Management Washington offers trash and garbage collection services, as well as recycling and landfill support across the state. They offer services to residential and commercial customers. They also offer information on recycling and waste reduction. They also provide information about the costs and public awareness of solid waste management. Continue reading to find out more.
Recycling
Washington's waste management system is increasingly reliant on recycling. In the past, the state's solid waste management program would ship three-quarters of all recyclable materials to China for processing. Nowadays, the majority of recyclables can be recycled in the state or within North America. The program assists communities and businesses in the Pacific Northwest to reduce and reuse as much waste as they can.
The state is implementing a system of fees for businesses that produce recyclable materials, requiring them to pay a fee based on the amount of waste they generate. These fees go toward Recycle BC to coordinate recycling efforts throughout the province.
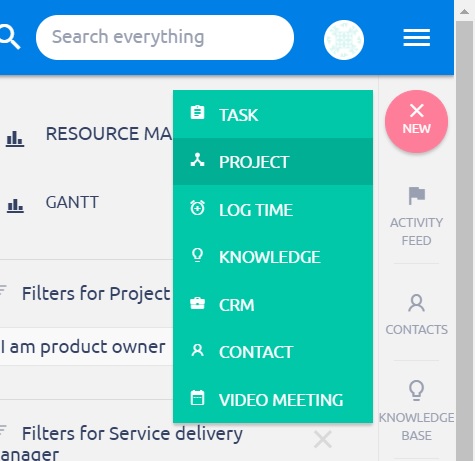
Public awareness
A new study revealed that Washington's waste management system is improving. According to the state's Department of Ecology, more than three pounds of garbage were recycled per person per day in 2013. According to the state's Department for Ecology, more than three pounds of garbage were recycled per person per day in 2013. This is an increase of one percent per year. There are still obstacles to recycling such as language barriers or infrastructure problems. Communities can adopt strategies such incentives, partnerships, or certifications in order to overcome these hurdles.
A key component of any waste management program is public awareness. Everybody must understand how to properly manage waste, as it is a result of human activity. It requires legislation that is strong and technical support as well as appropriate funding. Public participation is essential.
Prices
Washington, D.C.'s Public Transfer Stations have been losing money since years. The District's taxpayers have been paying upward of $50 per ton for waste removal. Although the District raised the cost by $10, it still increased its waste removal costs. The city is spending more than $50 Million a year on garbage collection.
The public transfer stations in the District are not economically viable and need to be renovated. Fort Totten station upgrades will be the District's top priority next year. This problem is made worse by the trash that's dumped in the suburbs.
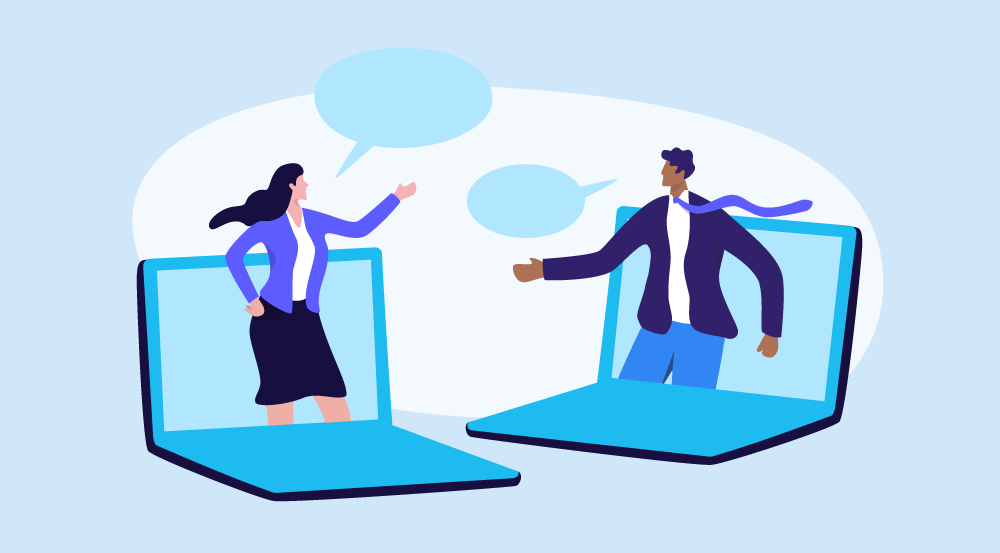
Companies involved with solid waste management
There are many companies in Washington State that handle solid waste. Sanitary Service is the largest company that handles solid waste. It collects and recycles trash. LeMay is another company offering solid waste collection services, recycling, and transport services. They also provide services such as site development, earth work, and more. GK Industrial Refuse Systems (Silver Springs Organics) are two other Washington companies involved in solid-waste management. Both companies are committed helping the environment by reducing waste.
The government involvement
Washington has a strong commitment in reducing waste and recycling. The state developed a solid-waste management plan to help meet this goal. This plan includes strategies to minimize waste, toxics, pollution and other harmful substances. The program permits large industrial projects. This allows Washington to minimize pollution and keep toxics out of the environment. Lastly, the plan outlines policies to help the public make better decisions about how to dispose of waste.
The Washington State Department of Ecology has set a goal to reduce food waste by 50 percent by 2030. This goal is comparable to both the U.S. and international targets. In late 2021 the department of ecology collaborated with other agencies and created a plan called Use Food Well Washington. The plan contains many policy recommendations and incorporates input from stakeholders.
FAQ
Six Sigma is so popular.
Six Sigma is easy to implement and can produce significant results. It provides a framework that allows for improvement and helps companies concentrate on what really matters.
What is a basic management tool that can be used for decision-making?
A decision matrix is a simple but powerful tool for helping managers make decisions. It helps them think systematically about all the options available to them.
A decision matrix can be used to show alternative options as rows or columns. This allows one to see how each alternative impacts other options.
This example shows four options, each represented by the boxes on either side of the matrix. Each box represents an alternative. The top row represents the current state of affairs, and the bottom row is indicative of what would happen in the event that nothing were done.
The effect of choosing Option 1 can be seen in column middle. It would translate into an increase in sales from $2million to $3million.
The following columns illustrate the impact of Options 2 and 3. These positive changes can increase sales by $1 million or $500,000. But, they also have some negative consequences. Option 2 can increase costs by $100 million, while Option 3 can reduce profits by $200,000.
The last column shows you the results of Option 4. This will result in sales falling by $1,000,000
The best thing about using a decision matrix is that you don't need to remember which numbers go where. It's easy to see the cells and instantly know if any one of them is better than another.
This is because your matrix has already done the hard work. It's simply a matter of comparing the numbers in the relevant cells.
Here's an example showing how you might use a Decision Matrix in your business.
Advertising is a decision that you make. You'll be able increase your monthly revenue by $5000 if you do. You'll also have additional expenses up to $10,000.
Look at the cell immediately below the one that states "Advertising" to calculate the net investment in advertising. It's $15,000. Advertising is worth much more than the investment cost.
What kind of people use Six Sigma?
Six sigma is a common concept for people who have worked in statistics or operations research. But anyone can benefit from it.
This requires a lot of dedication, so only people with great leadership skills can make the effort to implement it.
What is Kaizen?
Kaizen is a Japanese term meaning "continuous improvement." It is a philosophy that encourages employees to constantly look for ways to improve their work environment.
Kaizen is based upon the belief that each person should be capable of doing his or her job well.
It can sometimes seem difficult to make business decisions.
Businesses are complex systems, and they have many moving parts. The people who run them must juggle multiple priorities at once while also dealing with uncertainty and complexity.
To make good decisions, you must understand how these factors affect the entire system.
To do this, you must think carefully about what each part of the system does and why. It's important to also consider how they interact with each other.
You should also ask yourself if there are any hidden assumptions behind how you've been doing things. You might consider revisiting them if they are not.
Asking for assistance from someone else is a good idea if you are still having trouble. They may see things differently from you and have insights that could help you find a solution.
Statistics
- This field is expected to grow about 7% by 2028, a bit faster than the national average for job growth. (wgu.edu)
- 100% of the courses are offered online, and no campus visits are required — a big time-saver for you. (online.uc.edu)
- Our program is 100% engineered for your success. (online.uc.edu)
- The average salary for financial advisors in 2021 is around $60,000 per year, with the top 10% of the profession making more than $111,000 per year. (wgu.edu)
- The profession is expected to grow 7% by 2028, a bit faster than the national average. (wgu.edu)
External Links
How To
How do I get my Six Sigma License?
Six Sigma is a quality management tool to improve processes and increase efficiency. It is a method that enables companies to achieve consistent results with their operations. The name derives its meaning from the "sigmas" Greek word, which is composed of two letters that mean six. Motorola developed this process in 1986. Motorola recognized that they had to standardize their manufacturing processes to produce faster and more affordable products. There were many people doing the work and they had difficulty achieving consistency. They decided to use statistical tools like control charts and Pareto analysis to solve the problem. After this, they would apply these techniques to every part of the operation. This technique would enable them to make improvements in areas that needed it. When you are trying to obtain your Six Sigma certification, there are three steps. The first step is to find out if you're qualified. You'll want to take some classes and pass them before you start taking any tests. After passing the classes, you will be able to take the tests. It is important to review everything that you have learned in class. Once you have completed the class, you will be ready for the test. If you pass, you'll get certified. Finally, your certifications will be added to your resume.