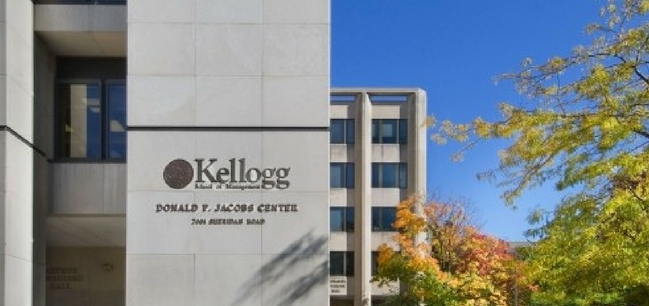
CSCMP stands for Certified Systems and Communications Manager, and it is a valuable certification for systems and communications professionals. CSCMP's 160 questions take four hours to complete. Pearson VUE is the independent testing company. Testing centers can be found worldwide. The test is proctored on-site and gives the taker a pass/fail score.
Academic membership
Academic membership is only available to full-time academic employees at accredited colleges and universities. This membership requires annual dues of $175 and provides opportunities to participate in collaborative forums and develop course content. This membership gives members an opportunity to network and meet colleagues in their field. We can help you get involved in the CSCM by providing details.
Membership fees
The Council of Supply Chain Management Professionals was established to connect, educate, and develop supply chain professionals all over the world. The group is $149 and you will have six months access to all the benefits and events that the organization offers. Young professionals can sign up to a 6-month membership starting at $88 Both membership options expire August 31, 2021.
A CSCMP membership includes access to the organization's resources, which include leading research and surveys. Members have access to the most recent research and valuable insights. The organization also hosts webinars, which are free to members. CSCMP membership allows you to learn more about supply chains management and improve your business operations.
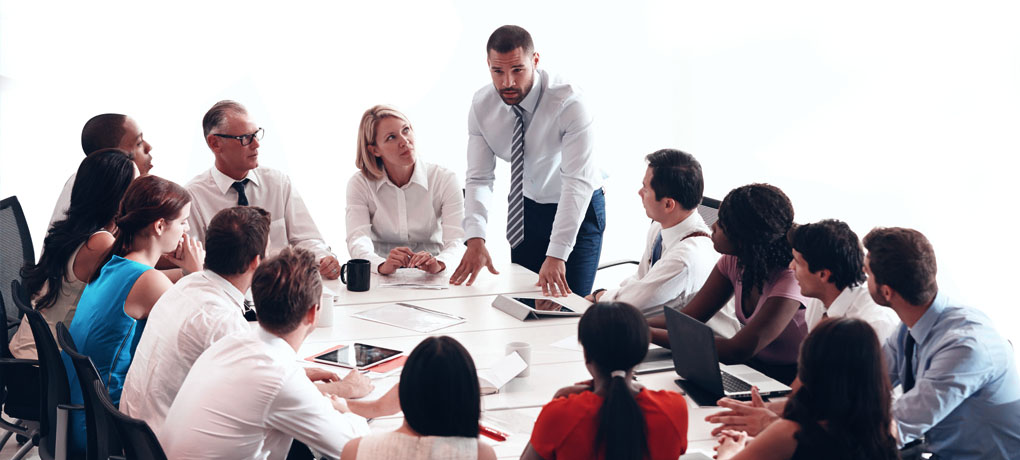
The SCMP level two exam is required to become a CSCMP membership. The exam can be taken within one year after you submit your membership fee. A confirmation email will be sent to you approximately one week before your scheduled test date.
FAQ
Why does it sometimes seem so hard to make good business decisions
Complex business systems have many moving parts. It is difficult for people in charge of businesses to manage multiple priorities simultaneously and also deal with uncertainty.
The key to making good decisions is to understand how these factors affect the system as a whole.
To do this, you must think carefully about what each part of the system does and why. It's important to also consider how they interact with each other.
You should also ask yourself if there are any hidden assumptions behind how you've been doing things. You might consider revisiting them if they are not.
Asking for assistance from someone else is a good idea if you are still having trouble. You might find their perspective is different from yours and they may have insight that can help you find the solution.
What are the most common errors made by managers?
Sometimes managers make it harder for their employees than is necessary.
They may not delegate enough responsibilities and not provide sufficient support.
In addition, many managers lack the communication skills required to motivate and lead their teams.
Managers sometimes set unrealistic expectations of their teams.
Managers may choose to solve every problem all by themselves, instead of delegating to others.
What role can a manager fill in a company’s management?
Different industries have different roles for managers.
In general, a manager controls the day-to-day operations of a company.
He/she will ensure that the company fulfills its financial obligations.
He/she ensures that employees follow the rules and regulations and adhere to quality standards.
He/she is responsible for the development of new products and services, as well as overseeing marketing campaigns.
What are the 3 basic management styles?
The three major management styles are authoritarian (left-faire), participative and laissez -faire. Each style has its strengths and weaknesses. Which style do YOU prefer? Why?
Autoritarian - The leader sets direction and expects everyone else to follow it. This style works best in large organizations that are stable and well-organized.
Laissez-faire is a leader who allows everyone to make their own decisions. This style is most effective when the organization's size and dynamics are small.
Participative – Leaders are open to suggestions and ideas from everyone. This is a great style for smaller organizations that value everyone.
Statistics
- Your choice in Step 5 may very likely be the same or similar to the alternative you placed at the top of your list at the end of Step 4. (umassd.edu)
- 100% of the courses are offered online, and no campus visits are required — a big time-saver for you. (online.uc.edu)
- As of 2020, personal bankers or tellers make an average of $32,620 per year, according to the BLS. (wgu.edu)
- The profession is expected to grow 7% by 2028, a bit faster than the national average. (wgu.edu)
- This field is expected to grow about 7% by 2028, a bit faster than the national average for job growth. (wgu.edu)
External Links
How To
How do I do the Kaizen Method?
Kaizen means continuous improvement. The term was coined in the 1950s at Toyota Motor Corporation and refers to the Japanese philosophy emphasizing constant improvement through small incremental changes. It's a process where people work together to improve their processes continuously.
Kaizen, a Lean Manufacturing method, is one of its most powerful. In this concept, employees who are responsible for the production line must identify problems that exist during the manufacturing process and try to solve them before they become big issues. This will increase the quality and decrease the cost of the products.
Kaizen is a way to raise awareness about what's happening around you. Correct any errors immediately to avoid future problems. It is important that employees report any problems they see while on the job to their managers.
There are some basic principles that we follow when doing kaizen. When working with kaizen, we always start with the end result and move towards the beginning. For example, if we want to improve our factory, we first fix the machines that produce the final product. Next, we fix the machines which produce components. Then, we fix those who work directly with the machines.
This is why it's called "kaizen" because it works step-by-step to improve everything. We finish fixing the factory and then go back to the beginning. This continues until we achieve perfection.
You need to know how to measure the effectiveness of kaizen within your business. There are many ways to tell if kaizen is effective. Another method is to see how many defects are found on the products. Another way is to check how much productivity has grown since kaizen was implemented.
If you want to find out if your kaizen is actually working, ask yourself why. Is it because the law required it or because you want to save money. You really believed it would make you successful?
Congratulations if you answered "yes" to any of the questions. Now you're ready for kaizen.