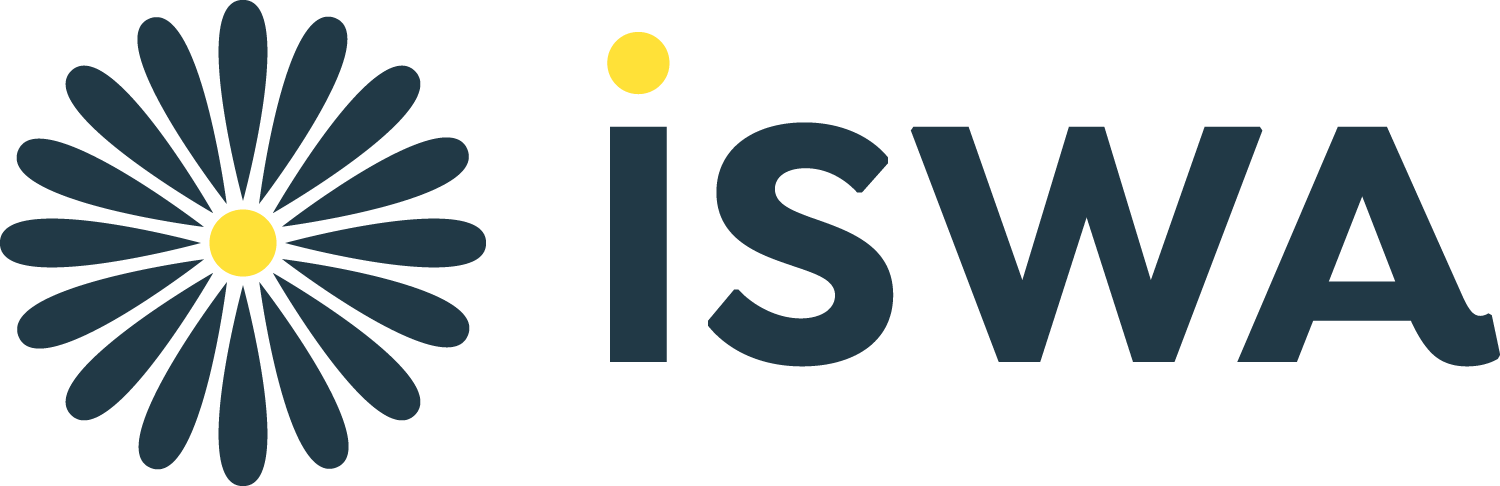
Consistency between contracts is crucial for construction projects involving multiple parties. Prime contracts often contain provisions that are passed on to subcontractors and other sub-subcontractors. Parties to a project should obtain a copy to verify that all agreements are in compliance.
Job order
Job order contracting is a way to manage projects and reduce costs. It can also be used to quickly respond to ongoing projects and clear any deferred maintenance. JOC offers more flexibility than other contracting options.
The job order contracting system makes the project owner and contractor more transparent right from the start. They know each others' work history and backgrounds and can trust each one. This helps reduce the number of change orders. Contractor and owner can develop a better relationship by understanding each other during contracting. This prevents miscommunications and errors from causing many changes.
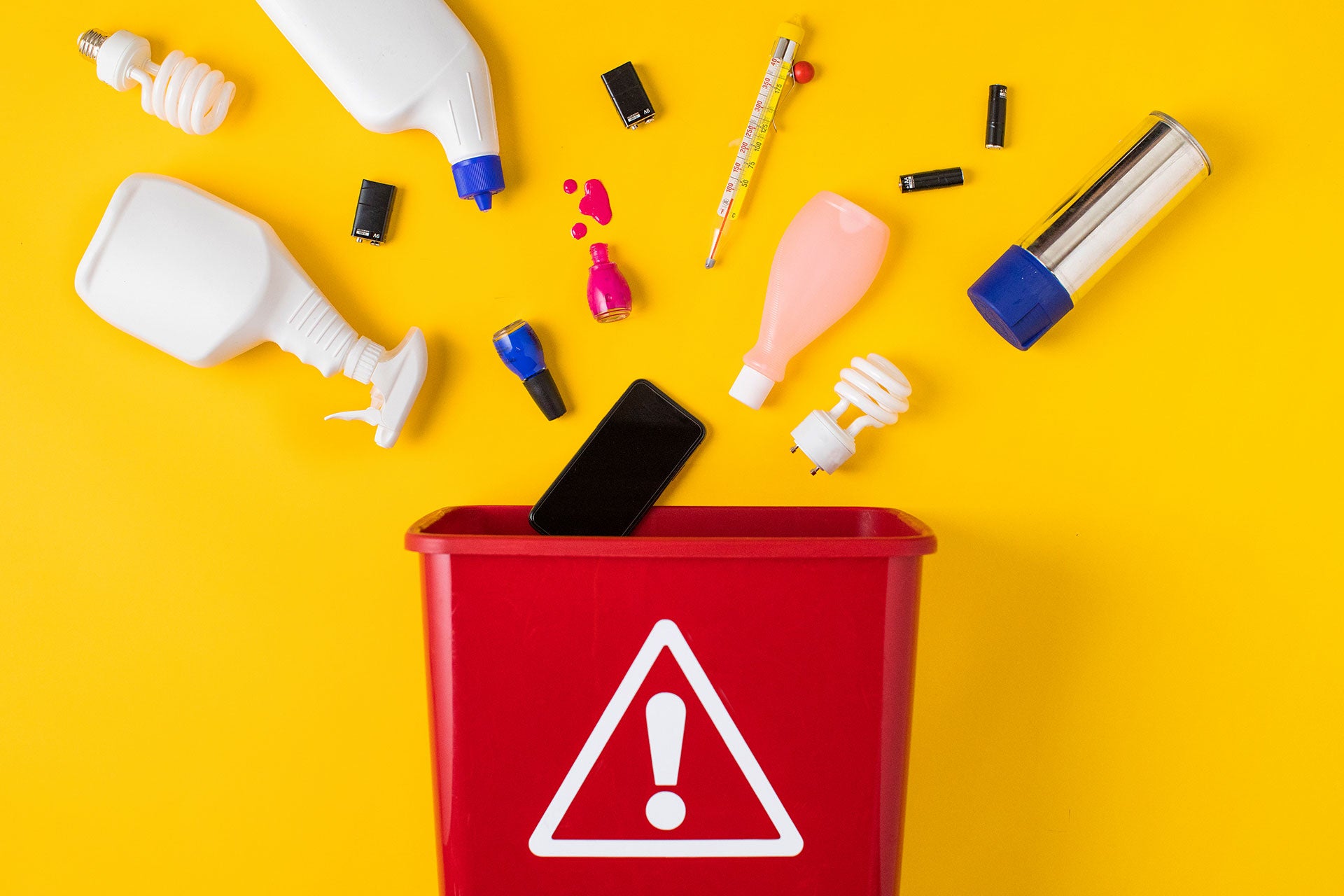
Incentive
Incentive contracting is a form of collaboration between a construction contractor and the client. The goal of incentive contracting is to maximize value for money. An incentive contract consists of two main parts: a share price and a cost target. A competitive process determines the target cost and should reflect the best estimate of project's final costs. Contractors are paid a fee to cover their overheads. The share formula introduces an incentive to the contract and determines how much should be divided between the parties.
Incentives contracts are great because they encourage accountability and transparency. By making sure that all stakeholders are aware of the work in progress, contractors are more likely to provide timely updates to owners. These updates encourage closer cooperation and allow for more skilled personnel assignments.
Lump-sum
Lump-sum contracting in construction is a way of contracting in which a fixed amount of money is agreed upon from the outset. This type of contract includes a fixed target and inputs as well as outputs. This type of contract is most effective when the project is clearly defined and has little variability. However, lump-sum contracting has its disadvantages.
This is because contractors have the option of hiding their profit margins. Moreover, contractors are not required to provide itemized bills of costs or quotes to the owner. One disadvantage to lump-sum contracts are that they can be subject to disputes or claims arising from poor contract terms. For instance, in some projects, the contractor may produce an unbalanced bid, in which unit prices are increased for items that are used later in the project. This could cause disputes about the payment rates.
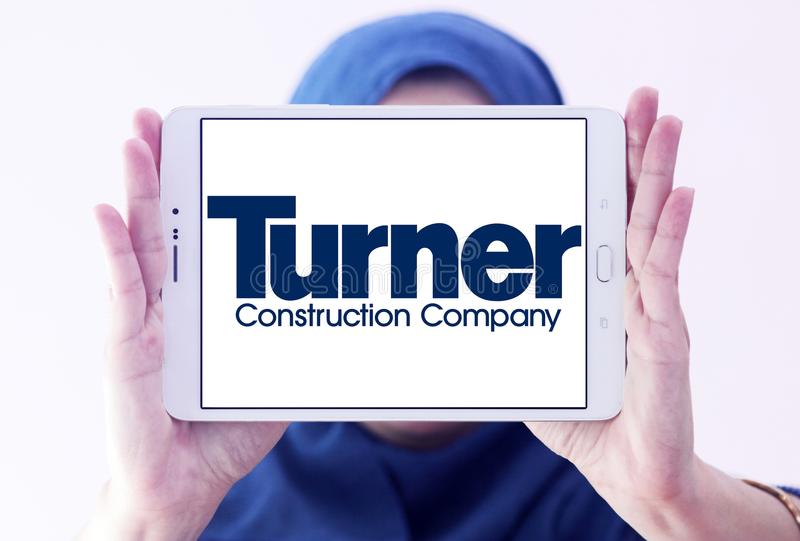
Delivery of integrated project services
Integrated Project Delivery, or IPD, is a new way of delivering construction projects. It removes any obstacles that could hinder project performance and aligns all stakeholders around a common goal. It increases the likelihood that projects will succeed by doing this. Implementing IPD means a change in traditional project management techniques and increased planning. IPD can be hindered by legal issues, mistrust among key players, and a lack in owner willingness. Many organizations and professional bodies in the built world are realizing the benefits IPD can bring and are starting smaller projects to implement it.
The advantages of IPD include the ability to complete projects faster and reduce costs. This method allows all parties to concentrate on their strengths, which leads to higher client satisfaction.
FAQ
What is the main difference between Six Sigma Six Sigma TQM and Six Sigma Six Sigma?
The key difference between the two quality management tools is that while six-sigma focuses its efforts on eliminating defects, total quality management (TQM), focuses more on improving processes and reducing cost.
Six Sigma can be described as a strategy for continuous improvement. It emphasizes the elimination or minimization of defects through statistical methods such control charts and p charts.
This method has the goal to reduce variation of product output. This is achieved by identifying and addressing the root causes of problems.
Total quality management involves measuring and monitoring all aspects of the organization. It also involves training employees to improve performance.
It is often used to increase productivity.
What is the role of a manager in a company?
Managers' roles vary from industry to industry.
In general, a manager controls the day-to-day operations of a company.
He/she ensures that the company meets its financial obligations and produces goods or services that customers want.
He/she will ensure that employees follow all rules and regulations, and adhere to quality standards.
He/she oversees marketing campaigns and plans new products.
What is Six Sigma, exactly?
It's a strategy for quality improvement that emphasizes customer care and continuous learning. The objective is to eliminate all defects through statistical methods.
Six Sigma was developed at Motorola in 1986 as part of its efforts to improve manufacturing processes.
This idea quickly spread throughout the industry. Today, many organizations use six sigma methods for product design, production and delivery.
What are the steps that management takes to reach a decision?
Managers have to make complex decisions. This involves many factors including analysis, strategy and planning, implementation, measurement and evaluation, feedback, feedback, and others.
The key thing to remember when managing people is that they are human beings just as you are and therefore make mistakes. You can always improve your performance, provided you are willing to make the effort.
This video will explain how decision-making works in Management. We discuss the different types of decisions and why they are important, every manager should know how to navigate them. Here are some topics you'll be learning about:
How do you manage employees effectively?
The key to effective management of employees is ensuring their happiness and productivity.
It also means having clear expectations of their behavior and keeping track of their performance.
Managers must be clear about their goals and those of their teams in order to succeed.
They need to communicate clearly with staff members. They should also ensure that they both reward high performers and discipline those who are not performing to their standards.
They should also keep records of all activities within their team. These include:
-
What was accomplished?
-
How much work did you put in?
-
Who did it?
-
It was done!
-
Why was this done?
This information is useful for monitoring performance and evaluating the results.
What are the top management skills?
Management skills are essential for any business owner, whether they're running a small local store or an international corporation. They are the ability to manage people and finances, space, money, and other factors.
Managerial skills are required when setting goals and objectives and planning strategies, leading employees, motivating them, solving problems, creating policies, procedures, or managing change.
As you can see, there's no end to the list of managerial duties!
What are some common mistakes managers make?
Sometimes managers make their job harder than they need to.
They may not assign enough responsibilities to staff members and provide them with inadequate support.
In addition, many managers lack the communication skills required to motivate and lead their teams.
Managers can set unrealistic expectations for their employees.
Managers might try to solve every problem by themselves rather than delegating the responsibility.
Statistics
- UpCounsel accepts only the top 5 percent of lawyers on its site. (upcounsel.com)
- Our program is 100% engineered for your success. (online.uc.edu)
- The profession is expected to grow 7% by 2028, a bit faster than the national average. (wgu.edu)
- This field is expected to grow about 7% by 2028, a bit faster than the national average for job growth. (wgu.edu)
- The average salary for financial advisors in 2021 is around $60,000 per year, with the top 10% of the profession making more than $111,000 per year. (wgu.edu)
External Links
How To
How is Lean Manufacturing done?
Lean Manufacturing is a method to reduce waste and increase efficiency using structured methods. They were developed in Japan by Toyota Motor Corporation (in the 1980s). The primary goal was to make products with lower costs and maintain high quality. Lean manufacturing focuses on eliminating unnecessary steps and activities from the production process. It is made up of five elements: continuous improvement, continuous improvement, just in-time, continuous change, and 5S. Pull systems involve producing only what the customer wants without any extra work. Continuous improvement means continuously improving on existing processes. Just-in-time refers to when components and materials are delivered directly to the point where they are needed. Kaizen is continuous improvement. This can be achieved by making small, incremental changes every day. Finally, 5S stands for sort, set in order, shine, standardize, and sustain. These five elements are used together to ensure the best possible results.
Lean Production System
Six key concepts form the foundation of the lean production system:
-
Flow is about moving material and information as near as customers can.
-
Value stream mapping - break down each stage of a process into discrete tasks and create a flowchart of the entire process;
-
Five S's: Sort, Shine Standardize, Sustain, Set In Order, Shine and Shine
-
Kanban - visual cues such as stickers or colored tape can be used to track inventory.
-
Theory of constraints: identify bottlenecks in your process and eliminate them using lean tools, such as kanban board.
-
Just-in Time - Send components and material directly to the point-of-use;
-
Continuous improvement: Make incremental improvements to the process instead of overhauling it completely.