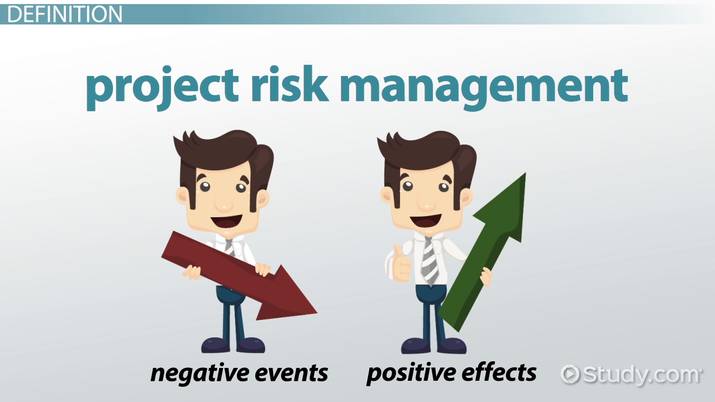
How can supply chain management be defined? Supply chain management is the process of managing commerce. It includes all aspects of the supply chain from raw materials to work-in process inventory to the final order fulfillment. The various aspects of supply chain management are discussed below. Let's take a look at four components of a supply network to help you better understand them. Here are some of the benefits that supply chain management can bring to your business.
Product portfolio planning
Portfolio planning is a tool that helps companies develop new products and manage inventories to meet changing market needs. Monitoring resource consumption is another aspect of this concept. Financial management is essential to manage current expenses and boost cash flow in slow seasons. Planning new products is often a collaborative effort between multiple departments in a company. If there are miscommunications or disconnections, it can be difficult to get the plan right. It is crucial to maintain open communication and keep track of targets to avoid this.
A company must look at its long-term business strategy and vision before it can implement a product range. The company can increase its sales and profits by aligning current projects with its long term goals. This will also help it gain market share. Portfolio planning allows companies to identify the most profitable products and give them the highest return on investments. They can also identify redundant products and cash cows.
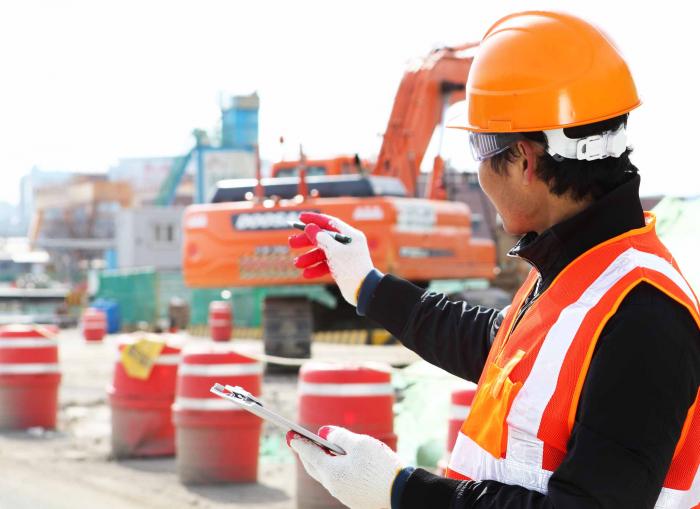
Distribution planning
Distribution planning, also known distribution requirements planning or DRP (for short), is a method that determines how many goods to produce and where to store them. This planning reduces the risk of shortages and lowers costs by taking into account how many products each region will need. It employs a tree-like structure for determining the gross requirements of a source of supply and the inventory required by each item. A DRP tool allows manufacturers to optimize key performance indicators and determine the best distribution plan.
Distribution planning is an integral component of supply chain management, and involves a number of sub-discipline practices that help to make the process more efficient. One of these practices is just-in-time inventories. Distribution is key to success because there are so many moving parts. It is crucial to have a strong distribution management strategy. This also requires real-time data. These are just a few of the components that make a distribution strategy successful.
Planning for sales and operations
S&OP (sales & operations planning) is a process that's used in supply chain control to coordinate activities among business units and achieve profitability. S&OP can take place on a monthly basis, an annual basis, or for two years. It involves forecasting, demand and supply planning, and executive reviews. The goal of this process is to deliver a better customer experience as well as improve the bottom-line. This process should not be limited to spreadsheets. It should be used by companies that have more than one location.
Regardless of the scale of the company, effective sales and operations planning will require strong leadership and a strong central figure. It is important to encourage cohesion among conflicting parts of the business. However, a central figure must be present to ensure that these standards are met. The leader of the sales department should be an active participant in the process, and his or her role should be to ensure that the process is carried out correctly.
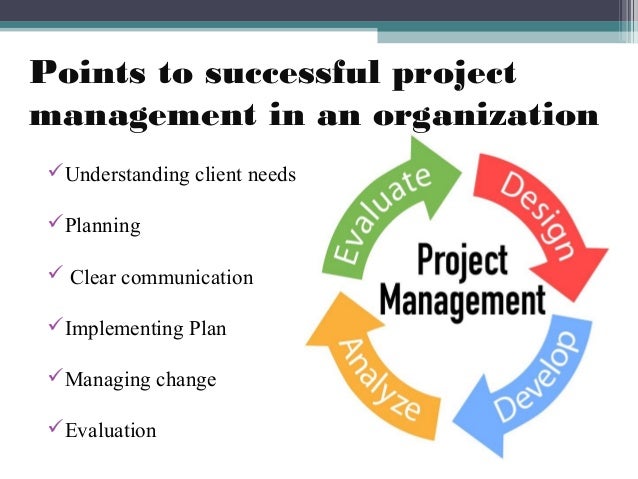
Planned trade promotion
Trade Promotion Planning can be a crucial part of any company's success. Trade promotion involves the marketing activity between a seller and manufacturer. This could include promotions, coupons and discounts that increase demand from retailers. In the end, this will lead to higher sales. Here are the fundamental elements of successful trade promotion planning. These are the key elements to a successful trade promotion program:
Promotion planning is a process for managing special events apart from a forecast. This planning process involves calculating the effects of a promotion using causal techniques and projecting these into designated periods in the future. This is used to develop marketing plans for repeated and one-off events. Consensus planning involves the use of multiple data sources in order to develop a consensus demand plan. It includes many different activities like safety stock planning, distribution plan, and outsourcing.
FAQ
Why does it sometimes seem so difficult to make good business decisions?
Complex systems are often complex and have many moving parts. The people who run them must juggle multiple priorities at once while also dealing with uncertainty and complexity.
Understanding how these factors impact the whole system is key to making informed decisions.
This requires you to think about the purpose and function of each component. You then need to consider how those individual pieces interact with each other.
It is also worth asking yourself if you have any unspoken assumptions about how you have been doing things. If so, it might be worth reexamining them.
For help, ask someone else if you're still stumped after all the above. You may be able to see things from a different perspective than you are and gain insight that can help you find a solution.
What are the steps that management takes to reach a decision?
The decision-making process for managers is complex and multifaceted. It includes many factors such as analysis, strategy planning, implementation and measurement. Evaluation, feedback and feedback are just some of the other factors.
Management of people requires that you remember that they are just as human as you are, and can make mistakes. You are always capable of improving yourself, and there's always room for improvement.
We explain in this video how the Management decision-making process works. We discuss different types of decisions as well as why they are important and how managers can navigate them. The following topics will be covered:
What are management principles?
Management concepts are the fundamental principles and practices that managers use when managing people and their resources. They cover topics like job descriptions (job descriptions), performance evaluations, training programmes, employee motivation and compensation systems.
What are the five management methods?
These five stages are: planning, execution monitoring, review and evaluation.
Planning involves setting goals for the future. Planning includes setting goals for the future.
Execution takes place when you actually implement the plans. It is important to ensure that everyone follows the plans.
Monitoring is a way to track progress towards your objectives. Regular reviews should be done of your performance against targets or budgets.
Reviews take place at the end of each year. They allow for an assessment of whether all went well throughout the year. If not, it is possible to make improvements for next year.
After the annual review is complete, evaluations are conducted. It helps to determine what worked and what didn’t. It also provides feedback on how well people performed.
What's the difference between Six Sigma and TQM?
The key difference between the two quality management tools is that while six-sigma focuses its efforts on eliminating defects, total quality management (TQM), focuses more on improving processes and reducing cost.
Six Sigma is a method for continuous improvement. This method emphasizes eliminating defects using statistical methods such p-charts, control charts, and Pareto analysis.
This method attempts to reduce variations in product output. This is achieved by identifying and addressing the root causes of problems.
Total quality management is the measurement and monitoring of all aspects within an organization. It also includes the training of employees to improve performance.
It is used to increase productivity.
What is Kaizen?
Kaizen refers to a Japanese term that stands for "continuous improvements." It is a philosophy which encourages employees in continuously improving their work environment.
Kaizen is based upon the belief that each person should be capable of doing his or her job well.
What kind of people use Six Sigma
Six sigma is a common concept for people who have worked in statistics or operations research. Anyone involved in business can benefit.
Because it requires a high degree of commitment, only leaders with strong leadership skills can implement it successfully.
Statistics
- This field is expected to grow about 7% by 2028, a bit faster than the national average for job growth. (wgu.edu)
- As of 2020, personal bankers or tellers make an average of $32,620 per year, according to the BLS. (wgu.edu)
- UpCounsel accepts only the top 5 percent of lawyers on its site. (upcounsel.com)
- 100% of the courses are offered online, and no campus visits are required — a big time-saver for you. (online.uc.edu)
- Hire the top business lawyers and save up to 60% on legal fees (upcounsel.com)
External Links
How To
What is Lean Manufacturing?
Lean Manufacturing uses structured methods to reduce waste, increase efficiency and reduce waste. They were created by Toyota Motor Corporation in Japan in the 1980s. The aim was to produce better quality products at lower costs. Lean manufacturing seeks to eliminate unnecessary steps and activities in the production process. It has five components: continuous improvement and pull systems; just-in time; continuous change; and kaizen (continuous innovation). Pull systems involve producing only what the customer wants without any extra work. Continuous improvement means continuously improving on existing processes. Just-in time refers to components and materials being delivered right at the place they are needed. Kaizen means continuous improvement. Kaizen involves making small changes and improving continuously. Last but not least, 5S is for sort. To achieve the best results, these five elements must be used together.
Lean Production System
Six key concepts form the foundation of the lean production system:
-
Flow - focuses on moving information and materials as close to customers as possible.
-
Value stream mapping - break down each stage of a process into discrete tasks and create a flowchart of the entire process;
-
Five S's, Sort, Set in Order, Shine. Standardize. and Sustain.
-
Kanban - visual cues such as stickers or colored tape can be used to track inventory.
-
Theory of constraints - identify bottlenecks during the process and eliminate them with lean tools like Kanban boards.
-
Just-in-time delivery - Deliver components and materials right to your point of use.
-
Continuous improvement - make incremental improvements to the process rather than overhauling it all at once.