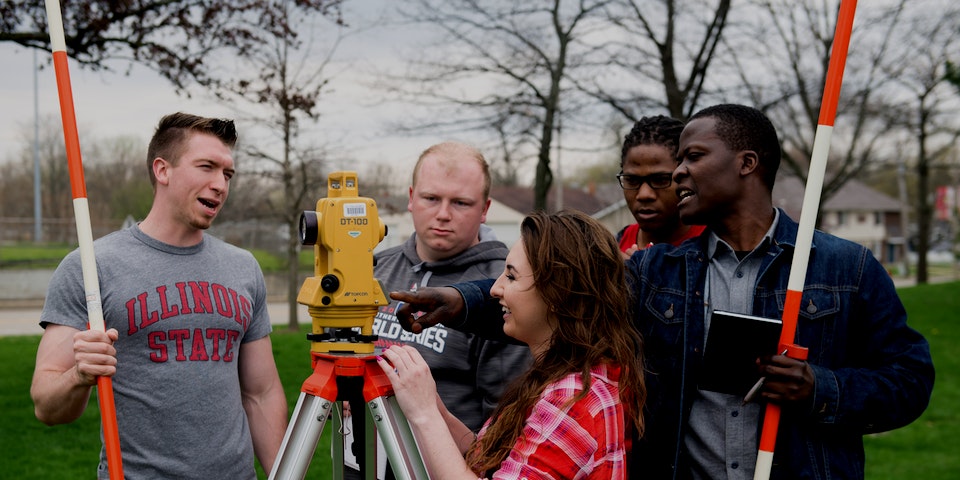
Logistics refers to the movement of goods from production to final delivery. Logistics involves many people, organizations, activities, information, and companies that make goods available for sale. A logistics supply chain is a collaborative effort between multiple stakeholders. While many companies focus on logistics alone, the process can include a variety of different components, such as transportation and software. Here are some examples of different logistical systems. These systems can be used to improve the supply chain operations of your company. Continue reading for more information.
Logistics is the movement of goods from production to delivery.
Logistics involves the efficient movement and storage of products from initial production to final delivery. By properly optimizing flows, products reach their customers at the right time, in the right place, at the right cost. Here are seven rights to logistics. The first is the right timing. Products should be delivered to customers on time, without delay, in the right condition.
Inbound logistics focuses on the inbound movement of materials and products to manufacturers, whereas outbound logistics focuses on the outbound flow of goods and information from sources outside of the business. Inbound logistic focuses on the acquisition of materials and the arrangement for inbound transportation, storage, delivery, and distribution to customers. Reverse logistics is the return shipment and packaging of finished products. It also includes the management of remaining inventory and, in certain cases, the disposal and reuse of waste.
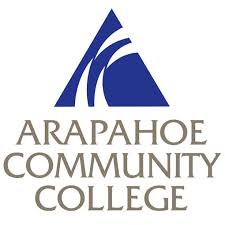
It is an ad-hoc business.
The term risk-adjusted investing (RAR), refers to the use of capital or funds that take on more risk than normal business investments. The opportunity cost of risk is the difference between risk-adjusted and normal business investment yields. RAR can reduce investment risk and assist business owners in managing cash flows across different business functions.
It is a limited part of a larger, collaborative supply chain
A highly integrated supply chain is a highly interdependent network of suppliers that rely on timely deliveries of quality components. Failure to deliver can cause the entire chain to stop. Even the most skilled suppliers and logistics providers can't prevent all disruptions. To ensure smooth and efficient operation of the chain, it is vital that everyone evaluates the potential risks involved in any given system.
Collaborations between manufacturers and retailers can have a positive impact on both parties. A recent example is the collaboration between a retailer, and a large U.S.-based retail chain. This resulted at a lower logistic cost between the factory to the store. This area of collaboration can help retailers increase sales. In this area, retailers and manufacturers can cooperate to reduce transport and labor expenses between the factory-store location.
It involves software
The use of supply management software helps companies manage their entire supply chain. The software handles all aspects of the supply chain, from vendor relationships to transactions. Supply chain management software should be used regardless of whether you run a small business or large corporation. These software can help you manage inventory and supplier relationships as well as flow of data within your company. These programs can cover all stages of product development including warehousing, shipping, and distribution. These programs can be used to manage inventory or provide insights into trends and consumer demand.
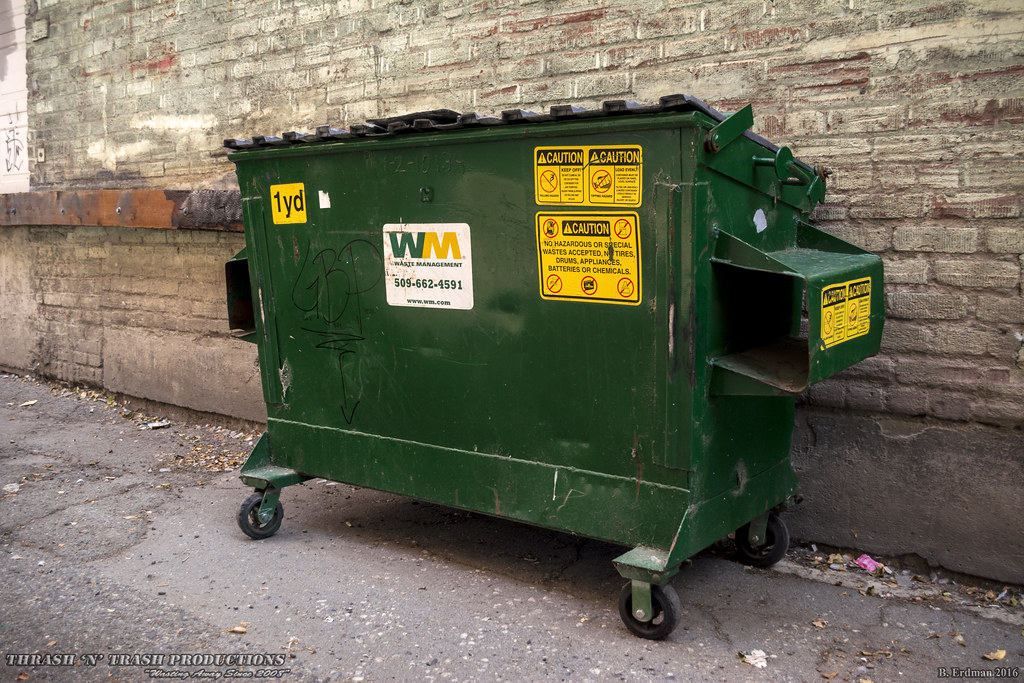
Software for logistics management can improve inventory management, real time fleet management, and streamline communication. It can also improve customer service. It automates daily tasks, and transforms data into useful insights for business owners. It helps improve communication and inventory management, which is crucial for successful supply chain management. These software can be used to improve customer service, and increase profitability. You might be curious about the benefits of purchasing software for your business.
FAQ
How do you effectively manage employees?
Managing employees effectively means ensuring that they are happy and productive.
It is important to set clear expectations about their behavior and keep track of their performance.
Managers need to establish clear goals for their team and for themselves.
They should communicate clearly to staff members. And they need to ensure that they reward good performance and discipline poor performers.
They must also keep records of team activities. These include:
-
What was the result?
-
How much work did you put in?
-
Who did it, anyway?
-
How did it get done?
-
Why?
This information is useful for monitoring performance and evaluating the results.
What are the three basic management styles?
There are three main management styles: participative, laissez-faire and authoritarian. Each style has its advantages and disadvantages. Which style do yo prefer? Why?
Autoritarian - The leader sets direction and expects everyone else to follow it. This style works best in large organizations that are stable and well-organized.
Laissez-faire: The leader lets each person decide for themselves. This approach works best in small, dynamic organizations.
Participative - The leader listens to ideas and suggestions from everyone. This style is most effective in smaller organizations, where everyone feels valued.
What are the key management skills?
Management skills are essential for any business owner, whether they're running a small local store or an international corporation. These skills include the ability of managing people, finances, time, space, and other factors.
You will need management skills to set goals and objectives, plan strategies, motivate employees, resolve problems, create policies and procedures, and manage change.
As you can see there is no end to the number of managerial tasks.
Statistics
- Your choice in Step 5 may very likely be the same or similar to the alternative you placed at the top of your list at the end of Step 4. (umassd.edu)
- As of 2020, personal bankers or tellers make an average of $32,620 per year, according to the BLS. (wgu.edu)
- 100% of the courses are offered online, and no campus visits are required — a big time-saver for you. (online.uc.edu)
- The BLS says that financial services jobs like banking are expected to grow 4% by 2030, about as fast as the national average. (wgu.edu)
- This field is expected to grow about 7% by 2028, a bit faster than the national average for job growth. (wgu.edu)
External Links
How To
How do you do the Kaizen method?
Kaizen means continuous improvement. This term was first used by Toyota Motor Corporation in the 1950s. It refers to the Japanese philosophy that emphasizes continuous improvement through small incremental changes. It's a process where people work together to improve their processes continuously.
Kaizen is one of the most effective methods used in Lean Manufacturing. Kaizen is a concept where employees in charge of the production line are required to spot problems during the manufacturing process before they become major issues. This improves the quality of products, while reducing the cost.
Kaizen is a way to raise awareness about what's happening around you. Correct any errors immediately to avoid future problems. If someone spots a problem while at work, they should immediately report it to their manager.
When doing kaizen, there are some principles we must follow. Start with the end product, and then move to the beginning. We can improve the factory by first fixing the machines that make it. Next, we repair the machines that make components. Then, the machines that make raw materials. And finally, we fix the workers who work directly with those machines.
This approach is called 'kaizen' because it focuses on improving everything steps by step. Once the factory is fixed, we return to the original site and work our way back until we get there.
To implement kaizen in your business, you need to find out how to measure its effectiveness. There are several ways to determine whether kaizen is working well. One method is to inspect the finished products for defects. Another way to find out how productive your company has been since you implemented kaizen is to measure the increase in productivity.
Another way to know whether kaizen is working is to ask yourself why did you decide to implement kaizen. Was it just because it was the law or because you wanted to save money? Did you really believe that it would be a success factor?
Congratulations if you answered "yes" to any of the questions. You're ready to start kaizen.