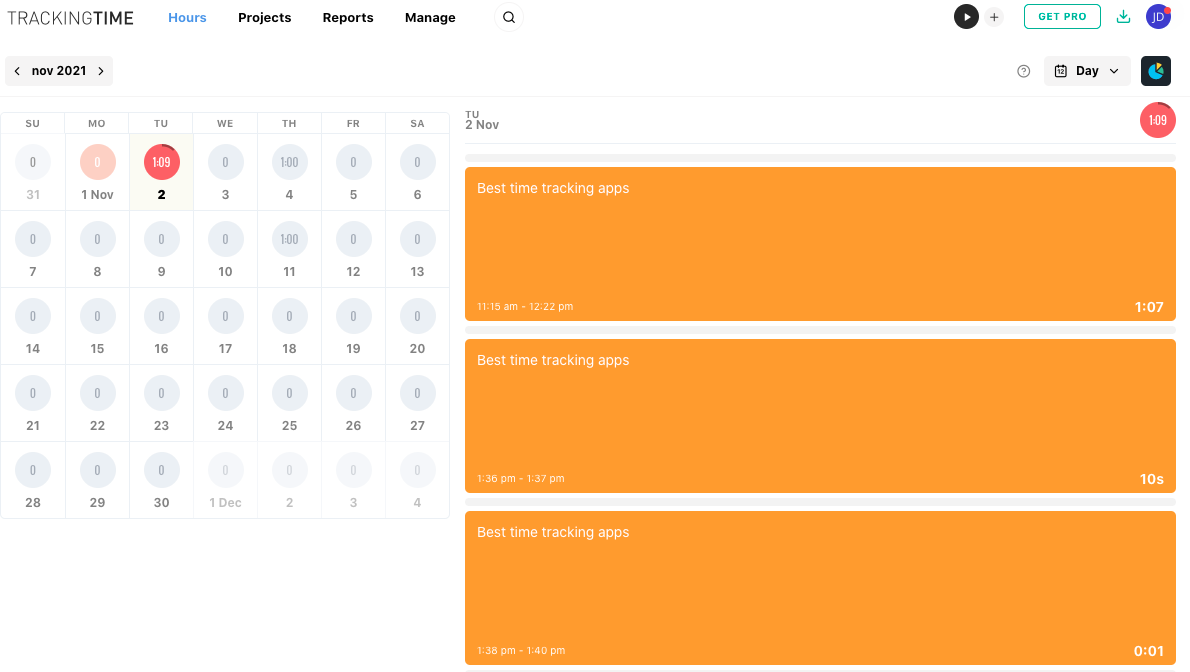
The undergraduate certificate program in facility management is designed for students who are interested in learning about multi-disciplinary facility operations. It comprises six hours of engineering, and six hours in non-engineering courses. The degree requires students to complete nine hours of coursework. Students must have completed at least two non-engineering classes outside of the College of Engineering. One course must be from within the College of Engineering. AEEN3350 is a requirement for the Certificate in facility management. The Department of Civil and Architectural Engineering offers program advice.
Salary ranges for both entry-level managers and experienced facilities managers
A facilities manager is responsible for the overall management of a building or complex, ensuring that it is healthy, safe, sustainable and fit for purpose. The salary for this role varies depending on the level of experience, but can be as high as $150,000 per year. An entry-level facility manager can expect to make between $40K-50K annually. Some companies offer performance-related bonus programs and profit sharing programs.
Facilities managers are responsible primarily for managing janitorial services. They also have responsibility for emergency preparedness. These jobs require leadership and management skills. Those with these skills often get promoted to higher positions. Although the pay scale for facilities managers varies depending upon their experience, there is great opportunity for upward mobility.
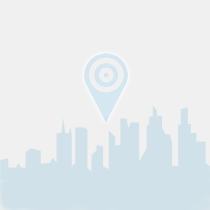
Requirements for obtaining u of t facility management certificate
The U of T Facility Management Certificate program is for professionals who want to coordinate human needs and the physical work environment. The program is a combination of principles from business administration and behavioral science. Students will learn about facility management topics such as design, construction and project management.
Both novice and experienced facility professionals can benefit from this program. It includes core management principles and provides practical tools and training that will help you improve the efficiency and performance of your work environment. It's available all year, and there are no prerequisites. Costs vary depending on professional background, IFMA membership status, and copy status. The certificate program includes a specialization on sustainability that focuses both on the economic and environmental aspects in building management.
Evaluation standards and policy
The U of T facility management certification program evaluation standards are based upon a variety of criteria that assess the program's quality and effectiveness. These standards are focused on the quality, integrity, effectiveness, and student experience. These standards are based upon feedback from students and other relevant constituencies. They can be used to guide planning and to make changes to the program.
Students who enroll in this certificate course learn how to critically assess and analyze program evaluations. They will be able to learn about different types of evaluation, such as cost-benefit analyses, process evaluations, and policy evaluations.
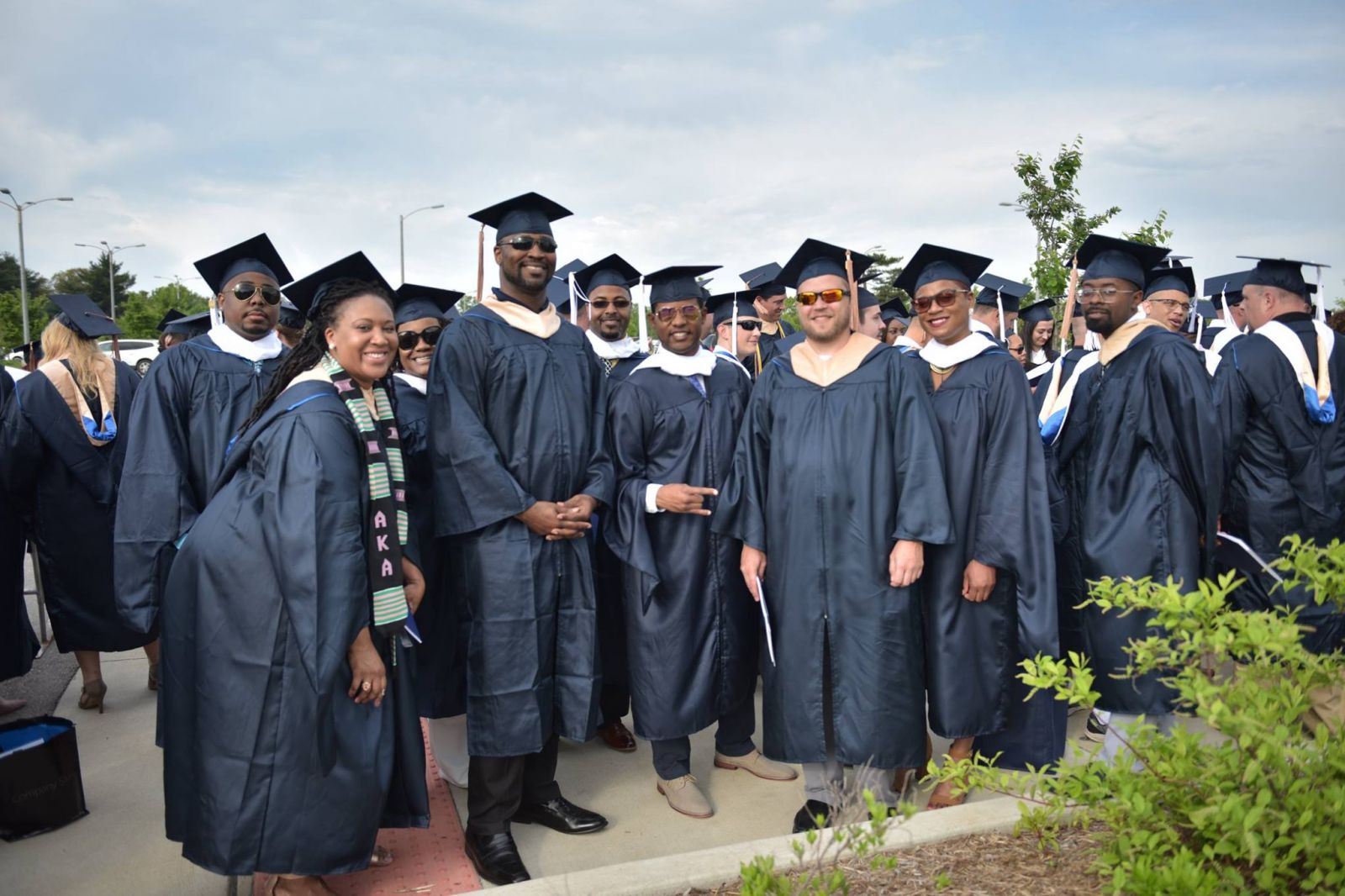
Cost of the certificate
The U of T's facility management certificate program will give you a broad overview of management. You will learn how to plan, manage, and optimize buildings' efficiency and cost effectiveness. Furthermore, you'll learn leadership, construction management and design. You'll also learn how to create and maintain a sustainable environment.
The U of T's facility management certificate program will prepare you to take a bachelor in construction management. No matter what type of building you manage, a facility management certificate will help you make them smarter and more sustainable. This includes knowing how best to prepare for emergencies as well as making sure the building is safe.
FAQ
What is a management tool to help with decision-making?
A decision matrix is an easy but powerful tool to aid managers in making informed decisions. It allows them to consider all possible solutions.
A decision matrix is a way to organize alternatives into rows and columns. This allows one to see how each alternative impacts other options.
In this example, there are four possible options represented by boxes on the left-hand side of the matrix. Each box represents an alternative. The top row depicts the current status quo, while the bottom row represents what would happen if no action was taken.
The effect of selecting Option 1 is shown in the middle column. It would translate into an increase in sales from $2million to $3million.
The effects of options 2 and 3 are shown in the next columns. These are positive changes - they increase sales by $1 million and $500 thousand respectively. These positive changes have their downsides. Option 2 can increase costs by $100 million, while Option 3 can reduce profits by $200,000.
The final column shows the results for Option 4. This will result in sales falling by $1,000,000
The best part of using a decision-matrix is that it doesn't require you to know which numbers belong where. Simply look at the cells to instantly determine if one choice is better than the other.
The matrix has already done all of the work. It's simply a matter of comparing the numbers in the relevant cells.
Here's a sample of how you might use decision matrixes in your business.
Decide whether you want to invest more in advertising. You'll be able increase your monthly revenue by $5000 if you do. However, additional expenses of $10 000 per month will be incurred.
The net result of advertising investment can be calculated by looking at the cell below that reads "Advertising." It is 15 thousand. Advertising is more valuable than its costs.
What are the five management process?
These five stages are: planning, execution monitoring, review and evaluation.
Planning involves setting goals for the future. It involves setting goals and making plans.
Execution happens when you actually do the plan. Everyone involved must follow them.
Monitoring is the act of monitoring your progress towards achieving your targets. This should involve regular reviews of performance against targets and budgets.
Each year, reviews are held at the end. They are a chance to see if everything went smoothly during the year. If not, then it may be possible to make adjustments in order to improve performance next time.
Evaluation takes place after the annual review. It helps identify what worked well and what didn't. It also gives feedback on how well people did.
How does a manager learn to manage?
You can improve your management skills by practicing them at all times.
Managers must continuously monitor the performance levels of their subordinates.
You should immediately take action if you see that your subordinate is not performing as well as you would like.
You should be able pinpoint what needs to improve and how to fix it.
What are the main styles of management?
The three basic management styles are: authoritarian, laissez-faire, and participative. Each style has strengths and flaws. Which style do yo prefer? Why?
Authority - The leader is the one who sets the direction and expects everyone in the organization to follow it. This style is most effective when an organization is large, stable, and well-run.
Laissez-faire – The leader gives each individual the freedom to make decisions for themselves. This style is most effective when the organization's size and dynamics are small.
Participative – The leader listens and takes in ideas from all. This style is most effective in smaller organizations, where everyone feels valued.
What is the difference in a project and program?
A program is permanent while a project can be temporary.
Projects usually have a goal and a deadline.
It is usually done by a group that reports back to another person.
A program usually has a set of goals and objectives.
It is usually done by one person.
How does Six Sigma function?
Six Sigma uses statistical analysis to find problems, measure them, analyze root causes, correct problems, and learn from experience.
The first step in solving a problem is to identify it.
The next step is to collect data and analyze it in order to identify trends or patterns.
Then, corrective actions can be taken to resolve the problem.
Finally, data is reanalyzed to determine whether the problem has been eliminated.
This continues until you solve the problem.
Statistics
- As of 2020, personal bankers or tellers make an average of $32,620 per year, according to the BLS. (wgu.edu)
- Your choice in Step 5 may very likely be the same or similar to the alternative you placed at the top of your list at the end of Step 4. (umassd.edu)
- 100% of the courses are offered online, and no campus visits are required — a big time-saver for you. (online.uc.edu)
- The average salary for financial advisors in 2021 is around $60,000 per year, with the top 10% of the profession making more than $111,000 per year. (wgu.edu)
- This field is expected to grow about 7% by 2028, a bit faster than the national average for job growth. (wgu.edu)
External Links
How To
How can you use the Kaizen method?
Kaizen means continuous improvement. Kaizen is a Japanese concept that encourages constant improvement by small incremental changes. It's a team effort to continuously improve processes.
Kaizen is one of Lean Manufacturing's most efficient methods. Employees responsible for the production line should identify potential problems in the manufacturing process and work together to resolve them. This increases the quality of products and reduces the cost.
The main idea behind kaizen is to make every worker aware of what happens around him/her. It is important to correct any problems immediately if they are discovered. Report any problem you see at work to your manager.
There are some basic principles that we follow when doing kaizen. The end product is always our starting point and we work toward the beginning. In order to improve our factory's production, we must first fix the machines producing the final product. We then fix the machines producing components, and the machines producing raw materials. We then fix the workers that work with those machines.
This method, called 'kaizen', focuses on improving each and every step of the process. Once we have finished fixing the factory, we return to the beginning and work until perfection.
You need to know how to measure the effectiveness of kaizen within your business. There are many ways you can determine if kaizen has been implemented well. One of these ways is to check the number of defects found on the finished products. Another method is to determine how much productivity has improved since the implementation of kaizen.
If you want to find out if your kaizen is actually working, ask yourself why. Was it just because it was the law or because you wanted to save money? It was a way to save money or help you succeed.
Congratulations! You're ready to start kaizen.