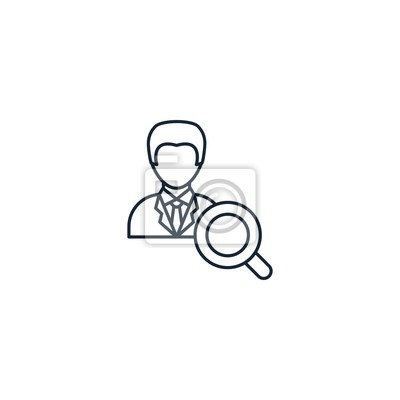
PMI templates are a great way to capture valuable feedback from project teams. These templates are great for many reasons. They can also be used to capture valuable feedback from project teams that have been completed. The following article includes information about PMI template and examples of formatting. It also discusses the costs associated with using these templates.
Template for project management
A PMI Project Management Template can speed up and simplify the process of creating a new project. This template contains a project management framework. It is a formal document that guides project execution and control. It is useful in documenting planning assumptions and facilitating communication between stakeholders. It includes a baseline schedule and major milestones that can be used to help you track progress and identify high-risk tasks.
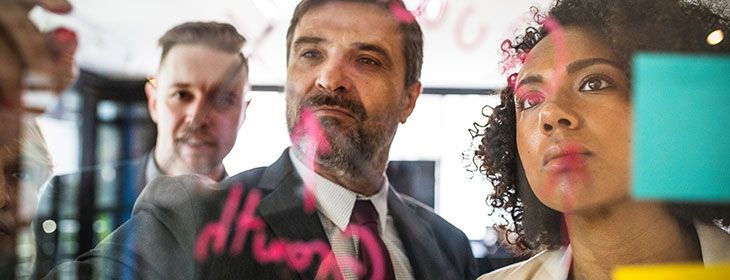
Here are some examples of wording
A Project Management Plan, or PMP, is a formal document which guides the execution and control a project. It includes a plan for the project's objectives and processes, and is an effective way to communicate with stakeholders. It documents the scope, cost and schedule baselines. It includes information about the major products and milestones, activities, goals, and other important details.
Formats
PMI templates simplify the process for creating project reviews. Although many templates are available for free download, registration is required. Once you've downloaded one you can edit the file and save it in whatever format you require. LibreOffice, an open-source alternative to Microsoft Office, is another option. Google Drive is another option. Google can convert any XLS file or doc file you upload to their servers.
Costs
Controlling costs is one of the most important features of a project management template. Using an appropriate template will allow you to easily track budgeted and actual costs and allocate resources appropriately. These templates include columns for labor costs, materials, and tasks and will show you how much money you need to spend on each category. The templates allow you to include pending costs and project sums.
Requirements for creation
Project Management Plan (PMP), a formal document, is used for project management and control. It contains planning assumptions, facilitates communication and documents approved scope and cost baselines. It also includes information about major products, milestones as well activities and objectives.
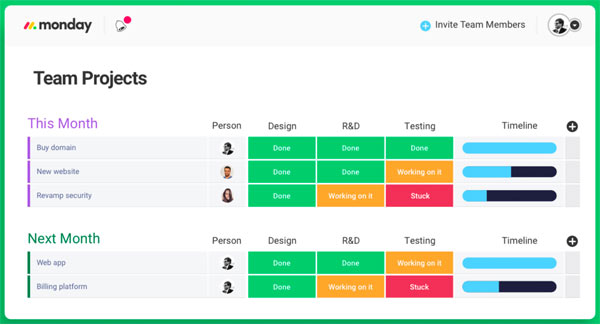
Getting a PMI
PMI requires all applicants to provide the entire scope of projects. For the PMP certification to be granted, you must have managed a project in a professional capacity. Both large and small projects can be listed in your application. However, make sure to emphasize your individual contributions. Use the PMBOK(r), Guide terminology if you have management experience.
FAQ
Six Sigma is so well-known.
Six Sigma is easy to implement and can produce significant results. It also provides a framework for measuring improvements and helps companies focus on what matters most.
What are the steps that management takes to reach a decision?
The decision-making process for managers is complex and multifaceted. It includes many factors such as analysis, strategy planning, implementation and measurement. Evaluation, feedback and feedback are just some of the other factors.
Remember that people are humans just like you, and will make mistakes. This is the key to managing them. As such, there are always opportunities for improvement, especially when you put in the effort to improve yourself.
This video shows you how management makes decisions. We will discuss the various types of decisions, and why they are so important. Every manager should be able to make them. The following topics will be covered.
What is the main difference between Six Sigma Six Sigma TQM and Six Sigma Six Sigma?
The major difference between the two tools for quality management is that six Sigma focuses on eliminating defect while total quality control (TQM), on improving processes and decreasing costs.
Six Sigma is an approach for continuous improvement. This method emphasizes eliminating defects using statistical methods such p-charts, control charts, and Pareto analysis.
The goal of this method is to reduce variation in product output. This is accomplished by identifying the root cause of problems and fixing them.
Total quality management involves measuring and monitoring all aspects of the organization. It also involves training employees to improve performance.
It is often used to increase productivity.
Statistics
- As of 2020, personal bankers or tellers make an average of $32,620 per year, according to the BLS. (wgu.edu)
- The average salary for financial advisors in 2021 is around $60,000 per year, with the top 10% of the profession making more than $111,000 per year. (wgu.edu)
- Your choice in Step 5 may very likely be the same or similar to the alternative you placed at the top of your list at the end of Step 4. (umassd.edu)
- The profession is expected to grow 7% by 2028, a bit faster than the national average. (wgu.edu)
- UpCounsel accepts only the top 5 percent of lawyers on its site. (upcounsel.com)
External Links
How To
How do you apply the Kaizen method to your life?
Kaizen means continuous improvement. Kaizen is a Japanese concept that encourages constant improvement by small incremental changes. It's a process where people work together to improve their processes continuously.
Kaizen is one method that Lean Manufacturing uses to its greatest advantage. This concept requires employees to identify and solve problems during manufacturing before they become major issues. This will increase the quality and decrease the cost of the products.
Kaizen is about making everyone aware of the world around them. Correct any errors immediately to avoid future problems. So, if someone notices a problem while working, he/she should report it to his/her manager.
When doing kaizen, there are some principles we must follow. The end product is always our starting point and we work toward the beginning. For example, if we want to improve our factory, we first fix the machines that produce the final product. Then, we fix the machines that produce components and then the ones that produce raw materials. Then, we fix those who work directly with the machines.
This method is known as kaizen because it focuses upon improving every aspect of the process step by step. We finish fixing the factory and then go back to the beginning. This continues until we achieve perfection.
You need to know how to measure the effectiveness of kaizen within your business. There are many methods to assess if kaizen works well. One of these ways is to check the number of defects found on the finished products. Another method is to determine how much productivity has improved since the implementation of kaizen.
If you want to find out if your kaizen is actually working, ask yourself why. It was because of the law, or simply because you wanted to save some money. Did you really think that it would help you achieve success?
Suppose you answered yes to any of these questions, congratulations! You are now ready to begin kaizen.