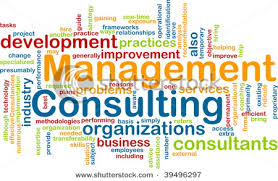
The management of waste is a key responsibility for businesses. It is a legal responsibility for businesses to dispose of their waste. It is vital for businesses that they recycle. However, every year there is still a lot waste. Businesses must also be accountable to the by-products of any processes they use. Businesses will be able to reduce waste by enforcing current laws and regulations. They can also create policies that will help them achieve their goals.
Environmental impact
Business waste management can have both a negative and positive impact on the environment. Properly disposing of garbage can lead to contamination of water supplies and surface areas. This can be dangerous for humans, animals, and plants. It can also pollute the air, which can cause respiratory problems and other health problems. To combat these issues, businesses should ensure that they are using environmentally-friendly methods of waste management.
Waste management companies are increasingly aware of the importance of environmental issues. Compliance with environmental regulations is vital for any business, no matter how small or large. This will improve the image of your business and help you to set a good example for other businesses. The best way to increase a business' environmental impact is to invest in recycling equipment.
Prices
Costs of waste management in business often include the costs of containers, labor, transfer vehicles, fuel, and landfill taxes. Recycling can have additional costs. Although recycling is not free, it is an effective way to manage waste. Many cities have recycling programmes that reduce the amount waste sent to landfills.
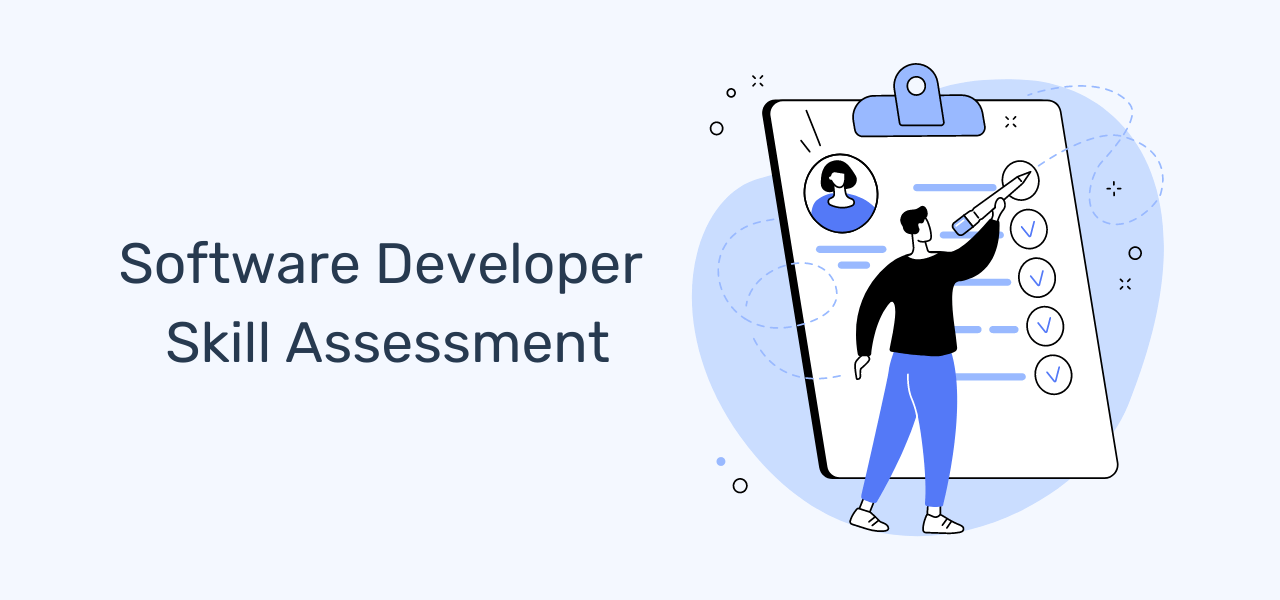
Recyclable waste can often be cheaper than traditional landfill fees. Over 60% of rubbish can also be recycled. There are strict regulations that the UK government enforces regarding waste disposal. If you don't comply, you could face fines or even jail sentence.
Problems
Poor waste management leads to climate change, pollution, and degradation of many ecosystems. Landfills, which are the last resort to dumping waste, emit methane, a powerful greenhouse gases linked with climate change. They also contaminate water and soil. In certain instances, a business might be responsible to creating more waste then it can handle.
Poor waste management is a health hazard that can increase the possibility of disease outbreaks. Solid waste that isn't properly managed can cause skin irritations, and even respiratory problems. It can also contaminate water sources and surfaces, causing food borne diseases. Landfills that aren't properly maintained can lead to a decline in the health of the local community. Toxic substances can leach into drinking water and cause serious health issues.
Solutions
Business waste management is vital as it helps keep the workplace cleaner and safer. This is especially important to companies working in the food and beverage industry. Good waste management plans can reduce potential fines and liability. It can also increase customer relationships and improve brand image. It is possible to stay ahead of the game by streamlining waste management.
Your waste management can be simplified by measuring it and identifying what percentage you generate. Consider investing in a large-scale vertical baler if your business produces a lot more cardboard waste. This will reduce the waste volume while making it easier to recycle.
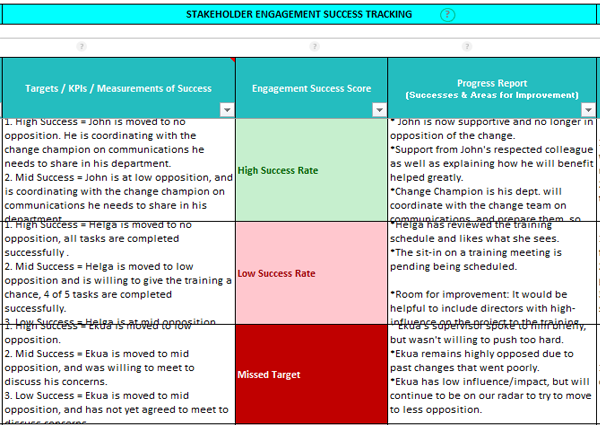
Partnering with a waste management company
Partnering with a waste management company for your business' waste management can be beneficial. You should make sure to choose companies that fit your schedule and provide consistent pickups and delivery. It is important to choose a waste disposal company that is well worth the investment.
The waste management firm you choose must be able and willing to work with you to schedule collections and provide estimates. They should also be easy to contact, and should have a strong customer-centric approach.
FAQ
What is a management tool to help with decision-making?
A decision matrix is an easy but powerful tool to aid managers in making informed decisions. They can think about all options and make informed decisions.
A decision matrix can be used to show alternative options as rows or columns. This allows one to see how each alternative impacts other options.
This example shows four options, each represented by the boxes on either side of the matrix. Each box represents an alternative. The top row displays the current situation, and the bottom row shows what might happen if nothing is done.
The effect of selecting Option 1 is shown in the middle column. It would translate into an increase in sales from $2million to $3million.
The next two columns show the effects of choosing Options 2 and 3. These positive changes result in increased sales of $1 million and $500,000. These changes can also have negative effects. Option 2 increases the cost of goods by $100,000. Option 3 decreases profits and makes them less attractive by $200,000.
The last column displays the results of selecting Option 4. This will result in sales falling by $1,000,000
The best thing about a decision matrix is the fact that you don't have to remember which numbers go with what. You just look at the cells and know immediately whether any given a choice is better than another.
This is because the matrix has already taken care of the hard work for you. It is as simple as comparing the numbers within the relevant cells.
Here's an example showing how you might use a Decision Matrix in your business.
You need to decide whether to invest in advertising. If you do this, you will be able to increase revenue by $5000 per month. You will still have to pay $10000 per month in additional expenses.
Look at the cell immediately below the one that states "Advertising" to calculate the net investment in advertising. It's $15,000. Therefore, you should choose to invest in advertising since it is worth more than the cost involved.
What are the 4 major functions of management
Management is responsible of planning, organizing, leading, and controlling people as well as resources. It includes creating policies and procedures, as well setting goals.
Management assists an organization in achieving its goals by providing direction, coordination and control, leadership, motivation, supervision and training, as well as evaluation.
The four main functions of management are:
Planning - This is the process of deciding what should be done.
Organizing - Organization involves deciding what should be done.
Directing - Directing is when you get people to do what you ask.
Controlling - Controlling means ensuring that people carry out tasks according to plan.
Which kind of people use Six Sigma
Six-sigma will be well-known to anyone who has worked in operations research or statistics. Anybody involved in any aspect or business can benefit.
It requires high levels of commitment and leadership skills to be successful.
What does Six Sigma mean?
Six Sigma employs statistical analysis to identify problems, measure them and analyze root causes. Six Sigma also uses experience to correct problems.
The first step in solving a problem is to identify it.
The data is then analyzed and collected to identify trends.
The problem is then rectified.
Finally, data is reanalyzed to determine whether the problem has been eliminated.
This cycle continues until there is a solution.
What can a manager do to improve his/her management skillset?
It is important to have good management skills.
Managers must constantly monitor the performance of their subordinates.
It is important to take immediate action if your subordinate doesn't perform as expected.
You should be able pinpoint what needs to improve and how to fix it.
What is TQM and how can it help you?
The industrial revolution led to the birth and growth of the quality movement. Manufacturing companies realized they couldn't compete solely on price. They had to improve efficiency and quality if they were to remain competitive.
In response to this need for improvement, management developed Total Quality Management (TQM), which focused on improving all aspects of an organization's performance. It included continuous improvement processes, employee involvement, and customer satisfaction.
Statistics
- The profession is expected to grow 7% by 2028, a bit faster than the national average. (wgu.edu)
- 100% of the courses are offered online, and no campus visits are required — a big time-saver for you. (online.uc.edu)
- The average salary for financial advisors in 2021 is around $60,000 per year, with the top 10% of the profession making more than $111,000 per year. (wgu.edu)
- Your choice in Step 5 may very likely be the same or similar to the alternative you placed at the top of your list at the end of Step 4. (umassd.edu)
- UpCounsel accepts only the top 5 percent of lawyers on its site. (upcounsel.com)
External Links
How To
How can you implement the Kaizen technique?
Kaizen means continuous improvement. This Japanese term refers to the Japanese philosophy of continuous improvement that emphasizes incremental improvements and constant improvement. It's a team effort to continuously improve processes.
Kaizen, a Lean Manufacturing method, is one of its most powerful. Kaizen is a concept where employees in charge of the production line are required to spot problems during the manufacturing process before they become major issues. This increases the quality of products and reduces the cost.
Kaizen is the idea that every worker should be aware of what is going on around them. If something is wrong, it should be corrected immediately so that no problem occurs. It is important that employees report any problems they see while on the job to their managers.
Kaizen has a set of basic principles that we all follow. The end product is always our starting point and we work toward the beginning. For example, if we want to improve our factory, we first fix the machines that produce the final product. Then, we fix the machines that produce components and then the ones that produce raw materials. Then we fix the workers, who directly work with these machines.
This approach is called 'kaizen' because it focuses on improving everything steps by step. Once we have finished fixing the factory, we return to the beginning and work until perfection.
How to measure kaizen's effectiveness in your business is essential to implement it. There are many methods to assess if kaizen works well. One method is to inspect the finished products for defects. Another way is determining how much productivity increased after implementing kaizen.
If you want to find out if your kaizen is actually working, ask yourself why. Did you do it because it was legal or to save money? Did you really believe it would lead to success?
If you answered yes to any one of these questions, congratulations! You are now ready to begin kaizen.