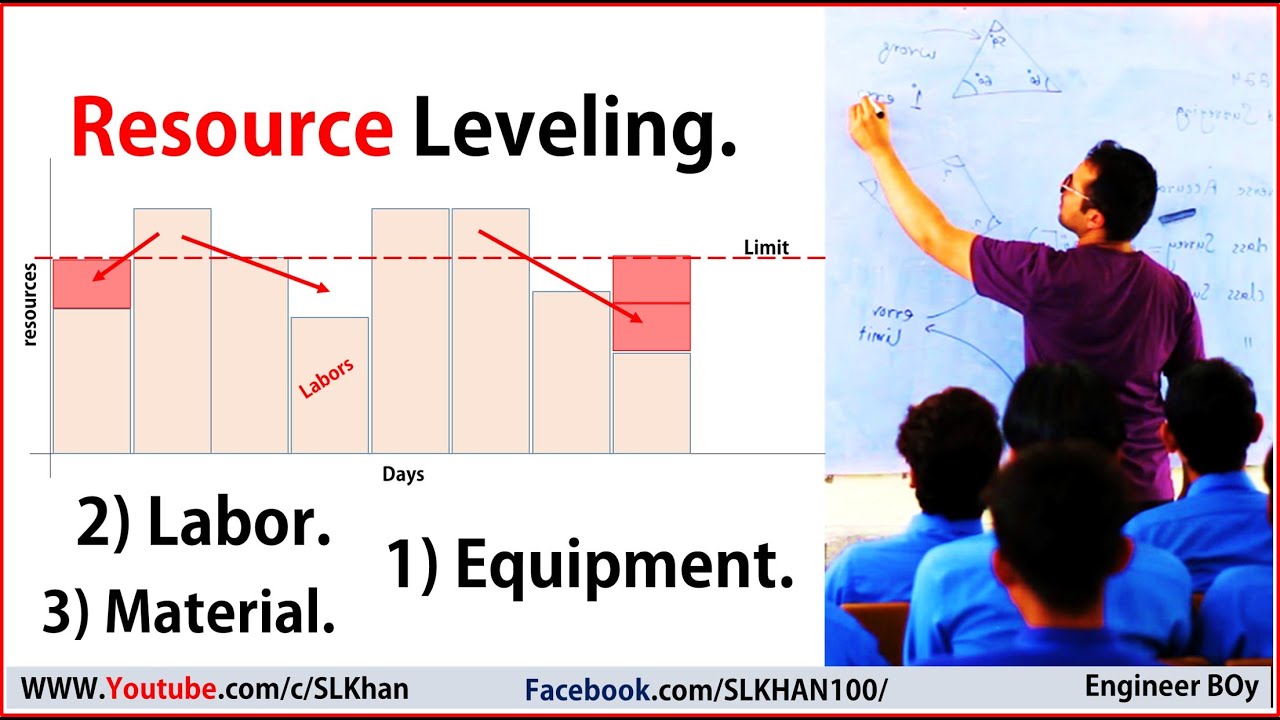
Crisis management is an integral part of an organization's strategy. It can either make or break an organization's performance. The success of a crisis management team depends on their ability to draw from their experiences and improve their practice. A number of psychological attributes are required for crisis managers to be successful, including task-oriented leadership behavior as well as communication plan and preparation. This article will explain these attributes and provide tips on how to prepare for crisis situations. This article will make you more equipped to manage a crisis.
Stress managers should be aware of their psychological characteristics
The psychological attributes of crisis managers are critical to the effectiveness of their role. They must be able communicate effectively, think rationally and not react too strongly to crisis situations. Empathy is one of the most important traits of crisis managers. Empathy can be described as the ability to see the situation from another person's perspective. Without it, they are unable to make informed decisions. They should be patient and avoid worrying.
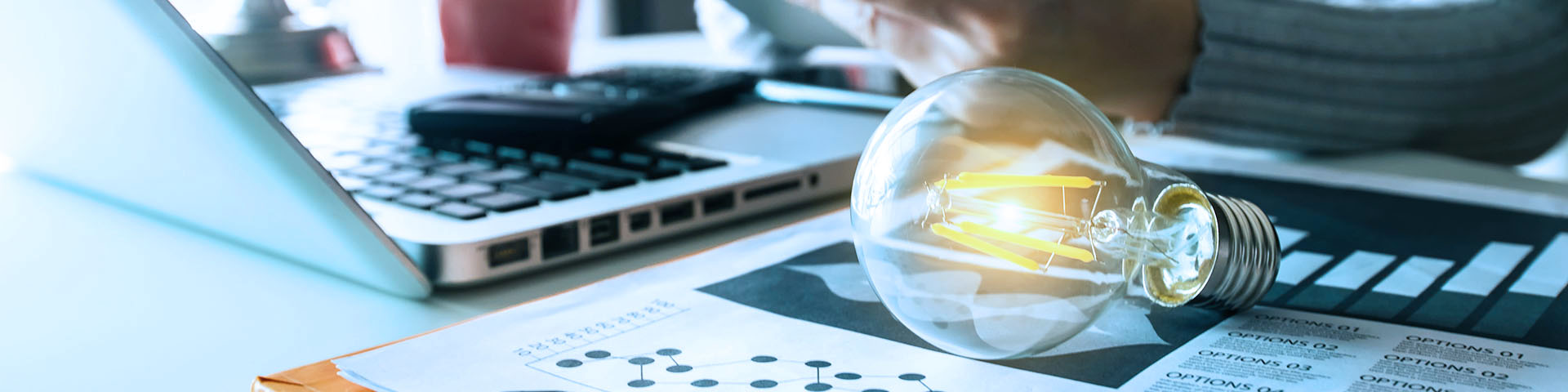
Leadership behavior that is task-oriented
Although task-oriented leaders can be a good choice, there are dangers. Task-oriented leadership can not only be counterproductive but can also lead to hostile work environments. In this article, we will look at some of the downsides of task-oriented leadership and how it can be detrimental to crisis managers. If you're in a situation where task-oriented leadership is necessary, here are some examples of when this style of leadership is not the best choice.
Preparedness for crises
Although crisis situations can happen to any organization they can be avoided by planning ahead. Crisis management practitioners recommend a thorough assessment of the organization's weaknesses and potential points of crisis. They also suggest conducting mock drills, and pre-drafting emergency messages. The crisis response team will be able to make the best decision possible by practicing before a crisis occurs. Read Crisis in Organizations II or Code Red in The Boardroom to learn more.
Communication plan
In order to develop a communications strategy for crisis managers, one of the most important steps is to establish a list for all parties. It is important to organize the information in a prioritized manner, so the most important customers are contacted first. You should also outline procedures for contacting suppliers during a crisis. This will enable you to communicate when you need, and not relying on inefficient manual processes.
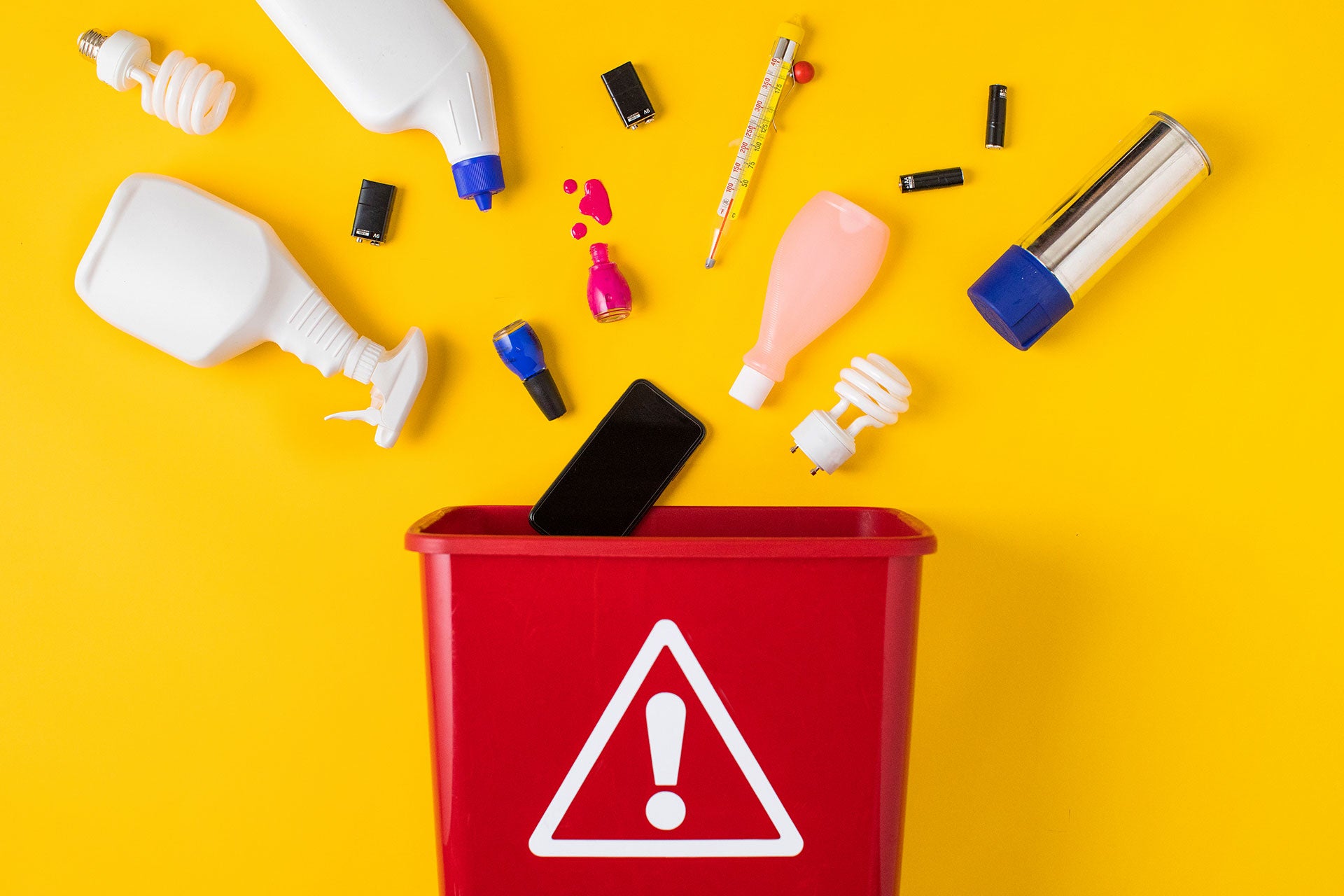
Public relations damage control
Avoiding PR problems is key if you want it to be handled properly. Even though small businesses may lack the funds to hire a crisis manager, they can follow a specific protocol to deal with public relations issues. Avoiding crises before they escalate can help you protect your business and reputation. A proactive approach to crisis management is more efficient and cost-effective than waiting until the controversy dies down.
FAQ
How do you manage your employees effectively?
Effectively managing employees means making sure they are productive and happy.
It is important to set clear expectations about their behavior and keep track of their performance.
Managers need clear goals to be able to accomplish this.
They should communicate clearly with employees. They should also ensure that they both reward high performers and discipline those who are not performing to their standards.
They should also keep records of all activities within their team. These include:
-
What did we accomplish?
-
What was the work involved?
-
Who did it?
-
It was done!
-
Why was it done?
This information can be used for monitoring performance and evaluating results.
How does Six Sigma work
Six Sigma uses statistical analysis for problems to be found, measured, analyzed root causes, corrected, and learned from.
The first step in solving a problem is to identify it.
Next, data are collected and analyzed in order to identify patterns and trends.
Next, corrective steps are taken to fix the problem.
Finally, data is reanalyzed to determine whether the problem has been eliminated.
This continues until the problem has been solved.
What is the difference between Six Sigma Six Sigma and TQM?
The main difference in these two quality management tools lies in the fact that six sigma is focused on eliminating defects and total quality management (TQM), emphasizes improving processes and reducing costs.
Six Sigma is a method for continuous improvement. It emphasizes the elimination or minimization of defects through statistical methods such control charts and p charts.
This method seeks to decrease variation in product output. This is done by identifying and correcting the root causes of problems.
Total quality management refers to the monitoring and measurement of all aspects in an organization. It also includes training employees to improve performance.
It is often used to increase productivity.
What's the difference between a program and a project?
A project is temporary while a programme is permanent.
A project typically has a defined goal and deadline.
It is often performed by a team of people, who report back on someone else.
A program is usually defined by a set or goals.
It is often implemented by one person.
What role should a manager play within a company
The role of a manager varies from one industry to another.
In general, a manager controls the day-to-day operations of a company.
He/she ensures the company meets its financial commitments and produces goods/services that customers demand.
He/she makes sure that employees adhere to the rules and regulations as well as quality standards.
He/she designs new products or services and manages marketing campaigns.
It can sometimes seem difficult to make business decisions.
Complex systems are often complex and have many moving parts. The people who run them must juggle multiple priorities at once while also dealing with uncertainty and complexity.
To make good decisions, you must understand how these factors affect the entire system.
It is important to consider the functions and reasons for each part of the system. It's important to also consider how they interact with each other.
Ask yourself if there are hidden assumptions that have influenced your behavior. You might consider revisiting them if they are not.
If you're still stuck after all this, try asking someone else for help. They may see things differently from you and have insights that could help you find a solution.
Why is it important that companies use project management methods?
Project management techniques can be used to ensure smooth project execution and meeting deadlines.
This is because many businesses depend heavily upon project work to produce products and services.
Companies must manage these projects effectively and efficiently.
Companies may lose their reputation, time and money if they do not have effective project management.
Statistics
- As of 2020, personal bankers or tellers make an average of $32,620 per year, according to the BLS. (wgu.edu)
- The BLS says that financial services jobs like banking are expected to grow 4% by 2030, about as fast as the national average. (wgu.edu)
- This field is expected to grow about 7% by 2028, a bit faster than the national average for job growth. (wgu.edu)
- Your choice in Step 5 may very likely be the same or similar to the alternative you placed at the top of your list at the end of Step 4. (umassd.edu)
- UpCounsel accepts only the top 5 percent of lawyers on its site. (upcounsel.com)
External Links
How To
How is Lean Manufacturing done?
Lean Manufacturing is a method to reduce waste and increase efficiency using structured methods. They were developed by Toyota Motor Corporation in Japan during the 1980s. The aim was to produce better quality products at lower costs. Lean manufacturing eliminates unnecessary steps and activities from a production process. It is composed of five fundamental elements: continuous improvement; pull systems, continuous improvements, just-in–time, kaizen, continuous change, and 5S. Pull systems are able to produce exactly what the customer requires without extra work. Continuous improvement is the continuous improvement of existing processes. Just-in-time is when components and other materials are delivered at their destination in a timely manner. Kaizen refers to continuous improvement. It is achieved through small changes that are made continuously. Five-S stands for sort. It is also the acronym for shine, standardize (standardize), and sustain. These five elements work together to produce the best results.
Lean Production System
Six key concepts form the foundation of the lean production system:
-
Flow - focus on moving material and information as close to customers as possible;
-
Value stream mapping: This is a way to break down each stage into separate tasks and create a flowchart for the entire process.
-
Five S's, Sort, Set in Order, Shine. Standardize. and Sustain.
-
Kanban - use visual signals such as colored tape, stickers, or other visual cues to keep track of inventory;
-
Theory of constraints - identify bottlenecks in the process and eliminate them using lean tools like kanban boards;
-
Just-intime - Order components and materials at your location right on the spot.
-
Continuous improvement is making incremental improvements to your process, rather than trying to overhaul it all at once.